ESP Mechanical Rehabilitation for Pulp and Paper Industry
Application
Industry: Pulp and Paper
ESP OEM / Information: Otokumpu, China / 2 Chambers (4 Fields)
Process: Multi-Fuel Boiler (MFB)
Country: North Sumatera, Indonesia
Problem
This ESP has been operating for more than 20 years. Many problems that could affect ESP performance were found during ESP Inspection done by Tai & Chyun engineer. They were cracked support insulator, damaged 1st layer inlet Gas Distribution (GD) screen, torn ESP casing, dust accumulation on Collecting Plate (CP), bent CP, missing CP, corroded CP, torn CP around rapping bar, broken rapping bar, missing Discharge Electrode (DE), alignment issue between CP and DE, worn out rapping hammer of both CP and DE, and worn out rapping bearing of both CP and DE.
Based on the abovementioned mechanical conditions, one out of the four fields, ESP-1 Field 2 could not operate due to short circuit issues. A minor repair had been done after inspection in order to normalize the particular field as a temporary solution.
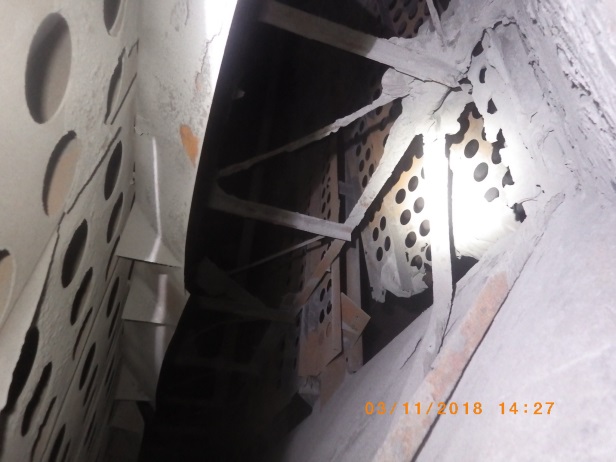
Damaged first layer inlet GD screen
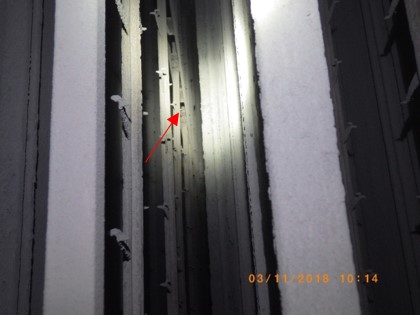
Close clearance between bent CP and DE system
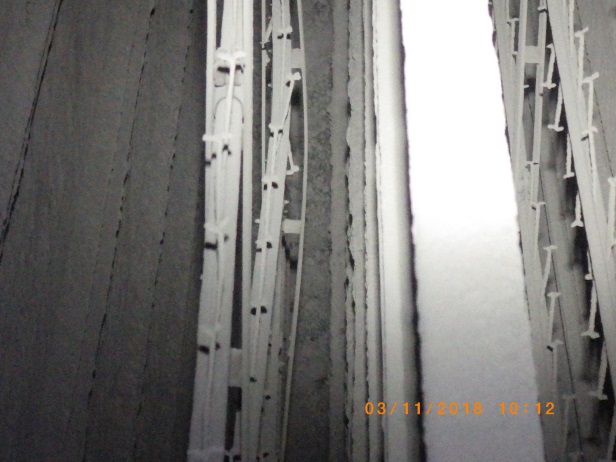
Damaged DE frame
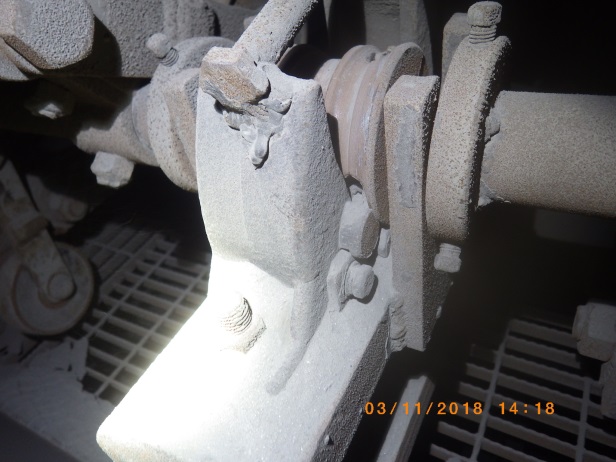
Worn-out CP bearing and shaft sleeve
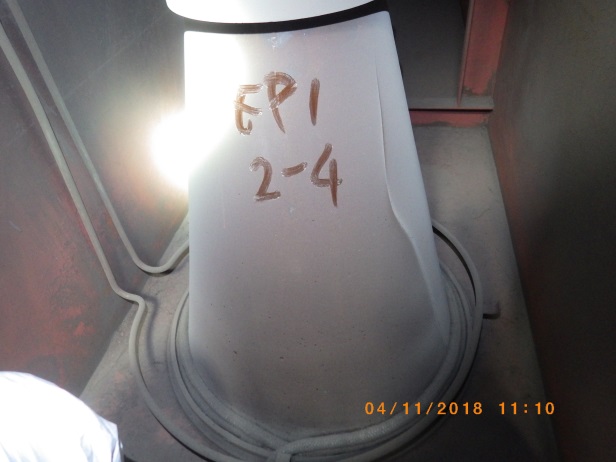
Cracked support insulator
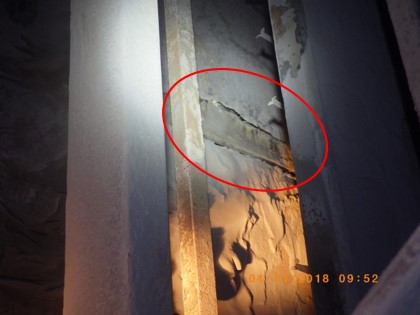
Torn ESP side wall behind first row CP
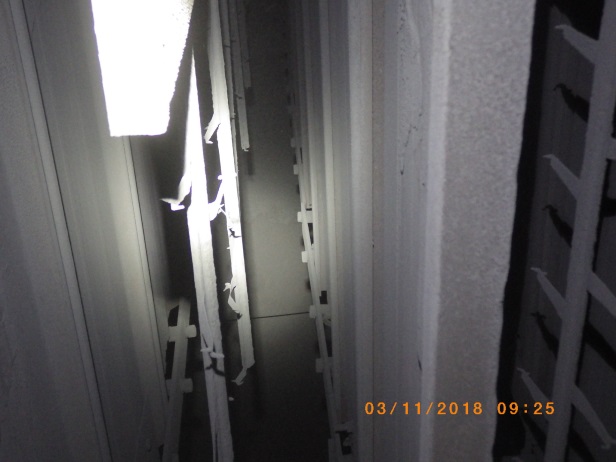
Bent and broken rapping bar
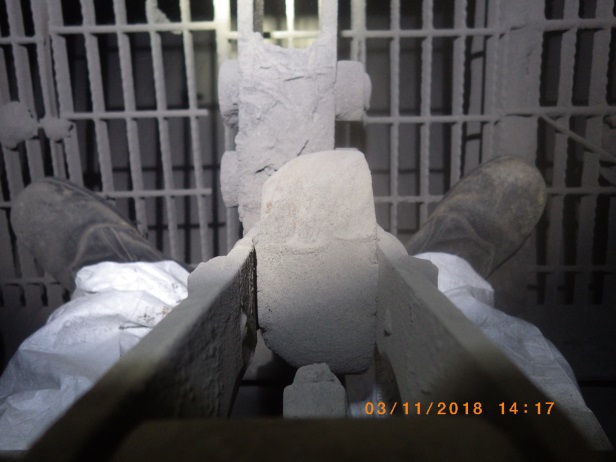
Worn-out CP hammer
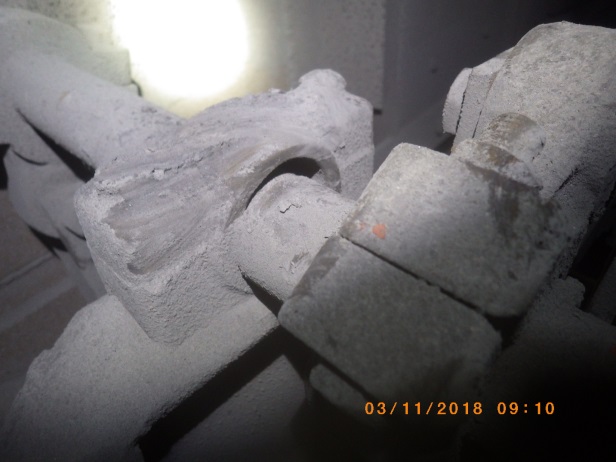
Worn-out CP bearing
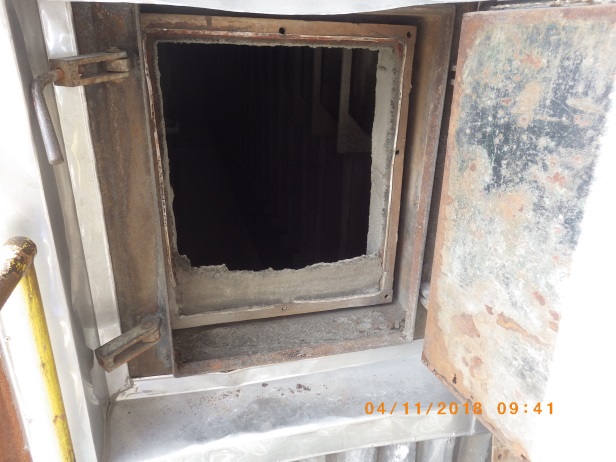
Dust accumulation around manhole area
Solution
Internal replacement was highly recommended by Tai & Chyun to fix the mentioned problems above and increase ESP dust colleting performance. The project for ESP-1 Field 2 rehabilitation was awarded to Tai & Chyun, which included the scope of parts supply; CP system, Rigid Discharge Electrode (RDE) system, CP rapping system, DE rapping system, support insulator, rapping insulator, GD screen and supervision for installation service.
Several problems were encountered during the project execution such as limited area for pre-assembly and lack of skillful contractor from the plant. Nevertheless, the project was completed within 15 days per end-user’s expectation during the 20-day shutdown period.
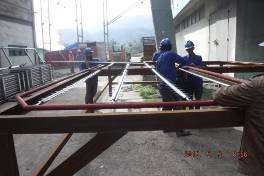
Pre-assembly RDE on the ground before shutdown
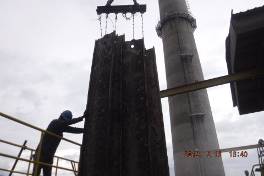
Multiple old CPs being lifted out of ESP using crane
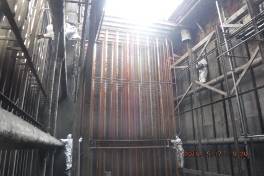
Positioning new DE frames
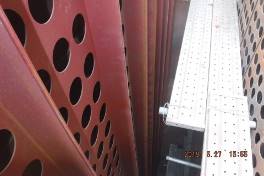
Newly installed GD screen
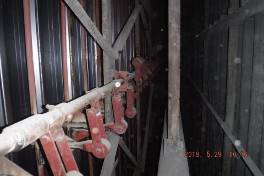
Rapping test for new DE rapping system
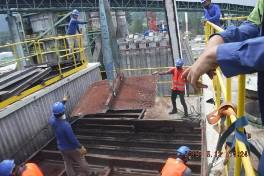
Dismantling hot roof
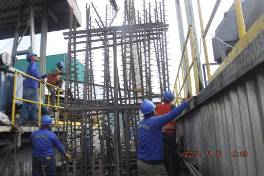
Old DE frames being taken out of ESP using crane
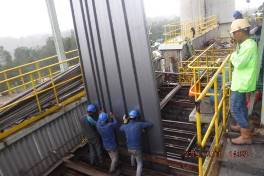
Multiple new CPs being lifted and inserted into ESP
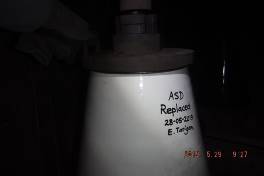
Newly installed support insulator
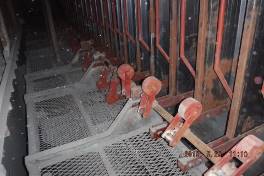
Rapping test for new CP rapping system
Benefit
No-load test of ESP-1 Field 2 had been carried out to ensure the quality of installation with the result of 51.6kV / 706mA at Transformer Rectifier (T/R) limitation of 80kV / 800mA. The load test result was also good, achieving 56kV / 800mA / 0spm at 7MW as shown in below V-I Curve and readings.
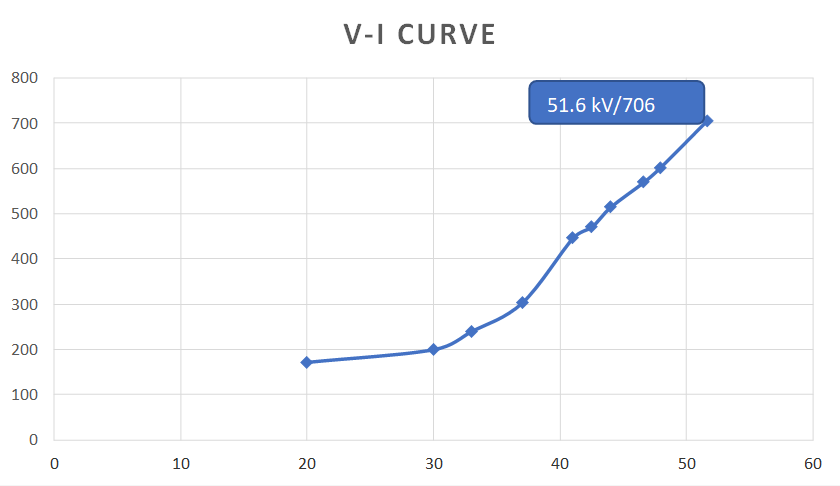
No-load test: V-I Curve of ESP-1 Field 2
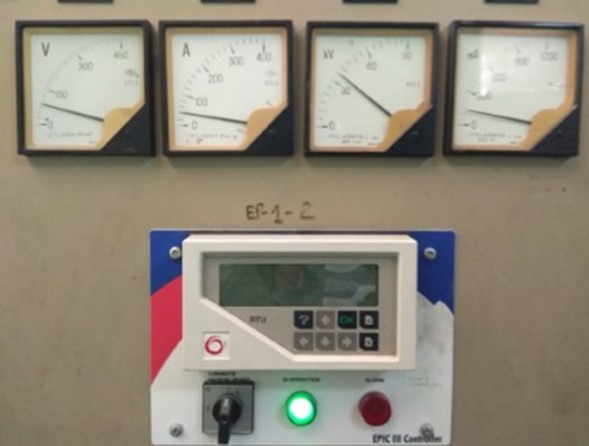
Readings: After minor repair
33.6kV ; 111mA ; 46SPM (full load boiler)
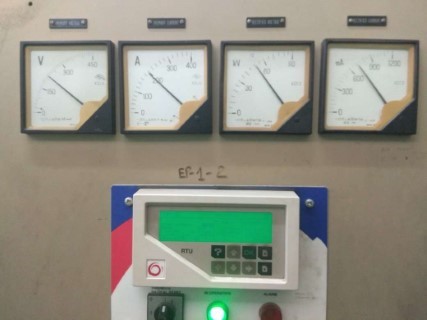
Readings: After internal replacement
56kV ; 800mA ; 0SPM (10% opacity at 7MW)
Based on overall readings of all 4-field MFB ESP, ESP-1 Field 2 internal replacement done by Tai & Chyun was satisfactory and plan for the next field replacement is on the way.
Field | Before replacement (Sept 2018) | After replacement (July 2019) |
ESP-1 Field 1 (Spiral DE) | 70kV ; 224mA | 62.3kV ; 281mA (hunting) |
ESP-1 Field 2 (RDE) | 32kV ; 5mA | 50kV ; 725mA ; 0spm |
ESP-2 Field 1 (Spiral DE) | 54kV ; 53mA | 60kV ; 180mA ; 0spm |
ESP-2 Field 2 (RDE) | 48kV ; 700mA | 46.6kV ; 498mA ; 39spm |
Note: T/R rating 72kV / 1200mA