ESP Retrofit (Concrete Rooftop) at Recovery Boiler
Application
Industry : Pulp & Paper
ESP OEM : ABB Flakt
Process : Recovery Boiler
Country : Thailand
Problem
A pulp & paper plant in Thailand has been operating since 1993. One of their recovery boiler ESPs’ efficiency has somehow declined due to its mechanical parts inside were worn out and, meanwhile, the boiler capacity has been increased by 33%. Problems found inside the ESP were misalignment between collecting plates and discharge electrode, worn out mechanical parts, and spark and arcing that limited ESP performance. The scraper in ash conveyor system sometimes got stuck from the fallen concrete which also created issues to the ESP. Though periodical maintenance was implemented, it seemed to not be able to overcome an inevitable deterioration.
Thus, an ESP rehabilitation was expected in response to the increasing production and to strengthen the operation reliability while reducing emission from the stack. Since the ESP rooftop was made of concrete, it was quite challenging to demolish and recover within the time period requirement.
Solution
ESP retrofit by Tai & Chyun was implemented to bring back the performance which we provided retrofit design, manufacture as well as technical direction during installation and commissioning for 1 unit of ESP. The project was completed within 47 days for retrofit and re-build of the entire 3 fields of ESP. We provided the new design of Rigid Discharge Electrode (RDE) to replace the original spiral design. The new RDE with its spikes generates more corona that increases the voltage to achieve better particulate collecting efficiency than the original spiral design does.
In addition, the width of Collecting Electrode (CE) was reduced while number of CEs increased. These methods do not affect ESP structure but provide convenience for future maintenance. In the 1st field where dust concentration is the highest and may lead to high spark and cause internal part damage, Tai & Chyun’s countermeasure was increasing the gap between CE and RDE by 50 mm to reduce spark issue and utilize the benefit of RDE to the maximum.
Original Design | New Design | |
Collecting Electrode (CE) | 750 mm width | 4 CEs per row | 480 mm width | 6 CEs per row |
Discharge Electrode (DE) | Spiral type
24 DEs per row |
Rigid Discharge Electrode (RDE)
12 DEs per row |
CE/DE gap in the 1st field | 250 mm | 300 mm |
Table 1: Comparison between original design before retrofit and new design after retrofit
Asides from the major part retrofit, Tai & Chyun also supplied new and replaced all mechanical internal parts such as rapping system, GD screen, etc., including ash conveyor system parts like scraper shafts together with technical supervision to ensure all parts have been installed correctly and alignment done properly.
Unlike common ESP where its rooftop is only made of steel plate for easy cutting and opening, the concrete rooftop ESP is time-consuming to be demolished. Tai & Chyun demolished the concrete and bent up the rebar to open up the roof area during installation and this rebar could be recovered after installation completed. With well-managed work execution, Tai & Chyun has been able to complete the job with extraordinary outcome.
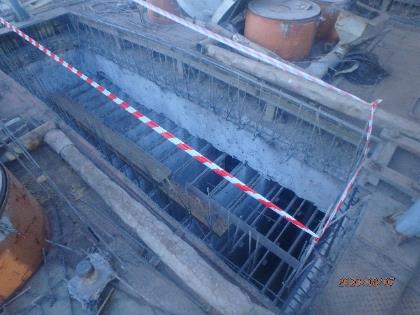
Demolished concrete and bent-up rebar in preparation for installation
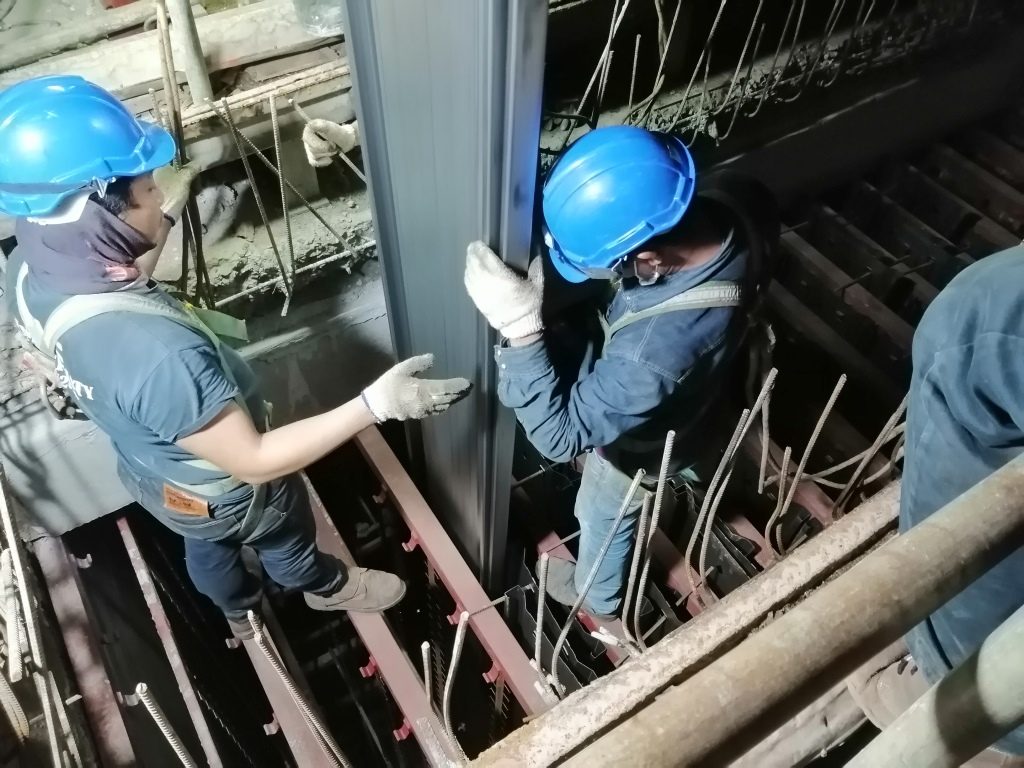
Installing new CE
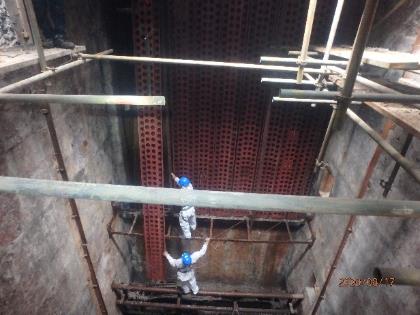
Installing new inlet GD screen
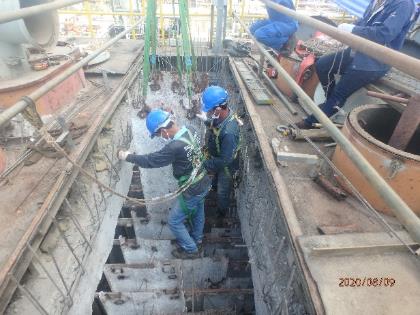
Dismantling internal parts
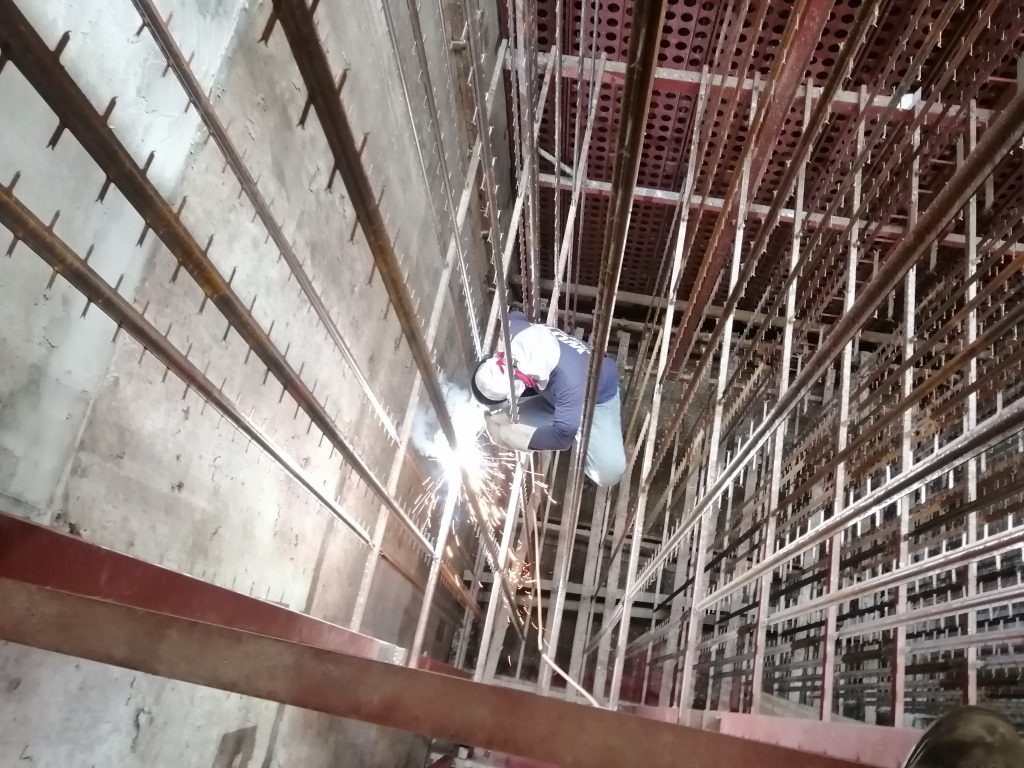
Installing new RDE
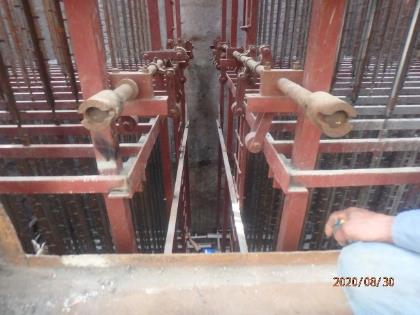
Newly installed rapping system
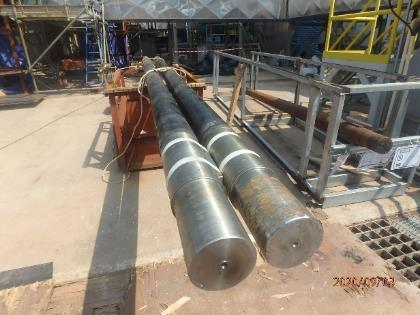
New scraper shaft installation
Benefit
ESP operation has become more reliable after retrofit. The emission test from outlet stack has been reduced to 32 mg/Nm3 despite the higher gas volume. Aging ESPs are facing the challenge in responding to the industry growth nowadays. Retrofitting an aging ESP does not only bring reliability back to its operation, but also a possibility to increase its performance beyond what it was originally designed for.
Gas Volume (Nm3/hr @ 7% O2) | Outlet Particulate (mg/Nm3) | |
Before Retrofit | 70,912 | 56 |
After Retrofit | 82,215 | 32 |
Table2: Emission test before and after retrofit from an accredited 3rd party certification