ESP Overhaul with Controller Upgrade in Coal-Fired Power Plant
Application
Industry: Power
ESP OEM: KC-Cottrell
Process: Power Boiler
Country: Rayong, Thailand
Problem
One of the coal-fired power plants in Rayong equipped with two large ESP units consisting of 24 fields and 2 chambers per unit operating at 660 MW capacity, hardened dust was found accumulated inside the ESP particularly in inlet and outlet nozzle area due to excessive ammonia from Selective Catalytic Reactor (SCR) during operation. Heavy sparking occurred in some fields, which limited dust collection efficiency. The hardened dust deposited on discharge electrode (DE) and collecting plate (CP) was hard to be removed by rapping system. If hardened dust continued to build up and eventually come into contact, ESP would trip. Meanwhile, transmitting pipeline in ash handling system was clogged with ash and some parts were damaged and found missing. The plant’s expectation was to recover its ESP dust collection efficiency and increase operation reliability.
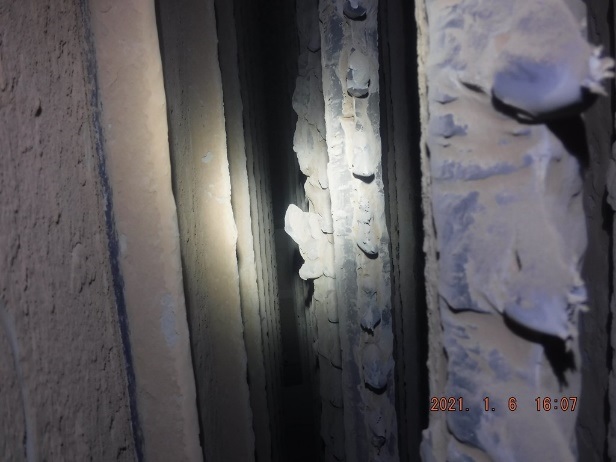
Dismantling the entire internal parts
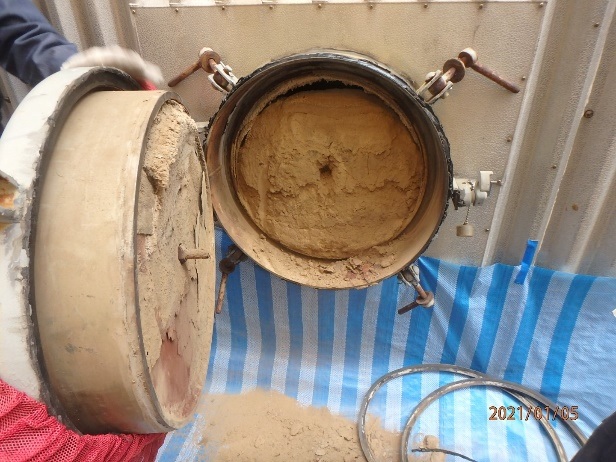
Hardened dust on access door
Solution
Tai & Chyun has been awarded for ESP inspection and maintenance during outage. The project included cleaning, inspection, and corrective maintenance for ESP as well as repair for ash handling system. Due to the hardened dust was hard to be dislodged by rapping system, manual cleaning had to be implemented during maintenance. Any bending, misalignment, detachment or crack inside ESP and hopper were inspected, repaired and replaced. Ash handling system has been cleaned, inspected and replaced for any broken or cracked parts.
In addition, Tai & Chyun supplied and upgraded 24 sets of controller in both units of ESP. 12 sets of GVC were installed in previous shutdown and the other 12 sets were installed in this project period. The new GDU keypad provides more informative data, intelligible readings and user-friendly operation.
The overhaul project for 24 fields of 2 units of ESP was completed within 25 days in both mechanical and electrical aspects. Upon project completion, Tai & Chyun performed no-load test to make sure that good performance of ESP had been achieved.
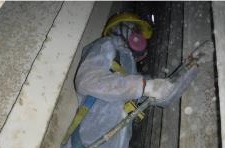
Hardened dust on CP and DE being manually cleaned
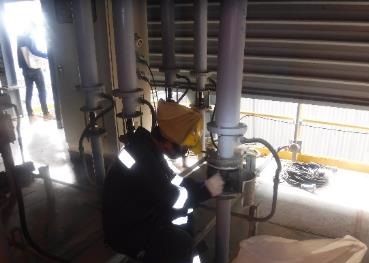
Replacement of broken boot seal clamp and MIGI alignment
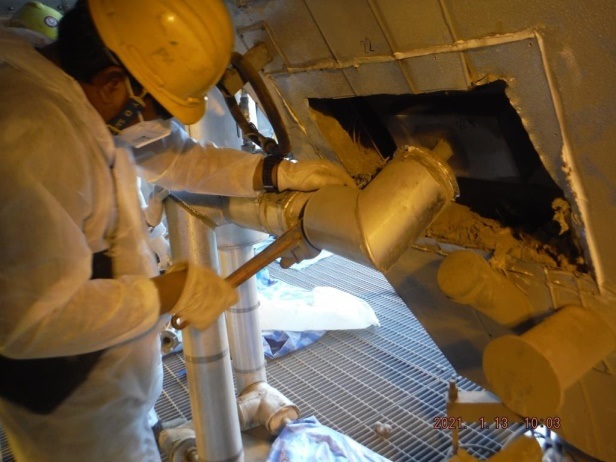
Cleaning and reinstallation of fluidizing stone
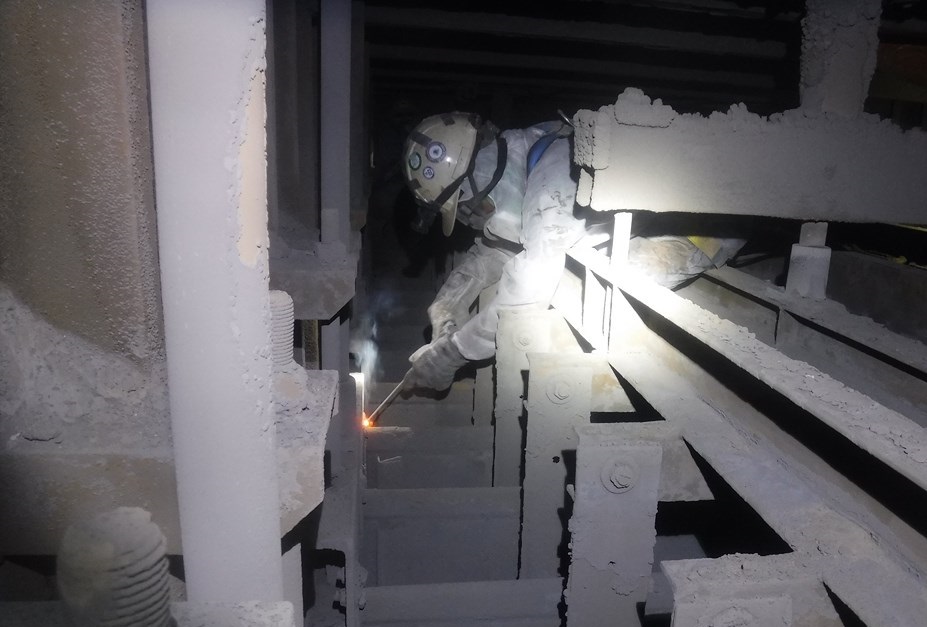
Cracked CP suspension beams being welded
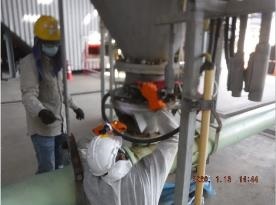
Cleaning and repair of Ash Handling System
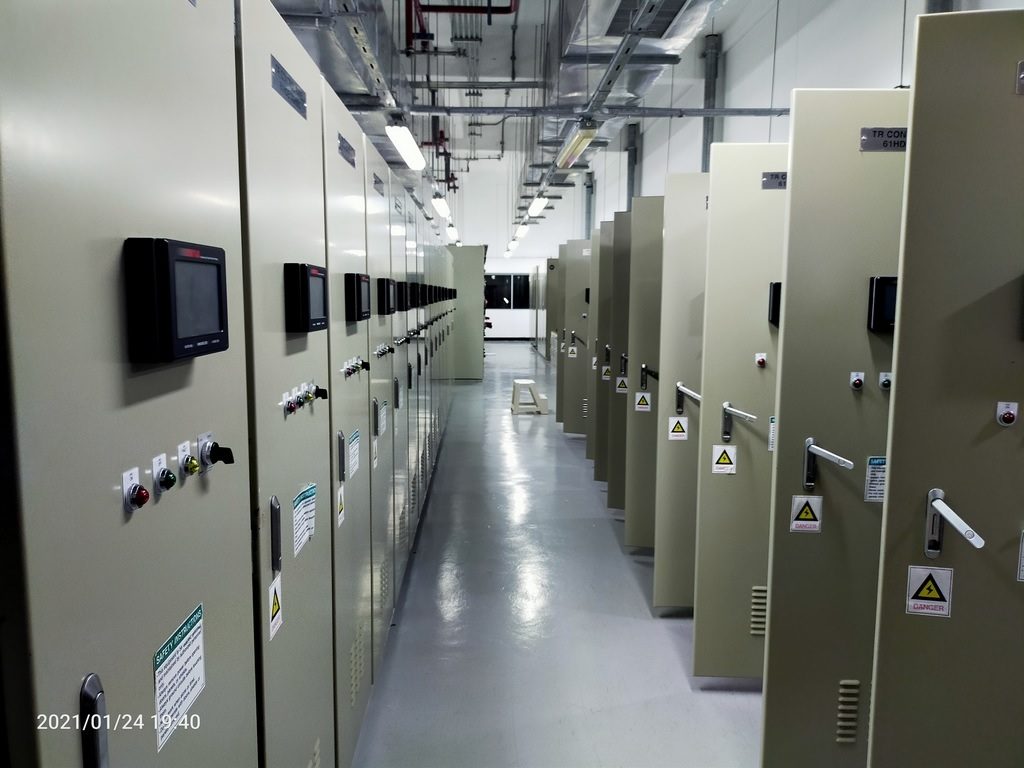
GDU keypad and GVC controller upgrade
Benefit
After maintenance, ESP operation has become more reliable and efficient even with higher loading. There has been no spark that limited the operation and mA value has increased to 108% leading to higher dust collection efficiency. Emission measured from the stack has been reduced to under 3 mg/Nm3. It is highly recommended to perform periodical ESP inspection and maintenance in order to keep your plant emission to the minimal.
Before
(Loading 78%) |
After
(Loading 95%) |
|
ESP unit A | 5.28 mg/Nm3 | 3 mg/Nm3 |
ESP unit B | 75.98 mg/Nm3 | 2 mg/Nm3 |
Table 1. Comparison of emission rate before and after maintenance
ESP Unit A |
Field | Before | After | ESP Unit B |
Field | Before | After | ||||||||
kV | mA | SPM | kV | mA | SPM | kV | mA | SPM | kV | mA | SPM | ||||
1 | 58 | 73 | 0 | 47 | 126 | 0 | 1 | 52 | 0 | 3 | 50 | 126 | 0 | ||
2 | 41 | 17 | 0 | 42 | 175 | 0 | 2 | 64 | 20 | 5 | 44 | 180 | 0 | ||
3 | 54 | 172 | 0 | 42 | 277 | 0 | 3 | 64 | 15 | 0 | 44 | 281 | 0 | ||
4 | 61 | 610 | 0 | 48 | 442 | 0 | 4 | 57 | 0 | 0 | 50 | 517 | 0 | ||
5 | 62 | 809 | 0 | 52 | 622 | 0 | 5 | 57 | 25 | 0 | 48 | 671 | 0 | ||
6 | 49 | 217 | 0 | 51 | 624 | 0 | 6 | 50 | 5 | 0 | 48 | 691 | 0 | ||
7 | 37 | 18 | 0 | 45 | 83 | 0 | 7 | 73 | 35 | 3 | 45 | 131 | 0 | ||
8 | 68 | 90 | 0 | 43 | 177 | 0 | 8 | 64 | 15 | 1 | 42 | 118 | 0 | ||
9 | 62 | 221 | 9 | 44 | 272 | 0 | 9 | 61 | 105 | 4 | 45 | 277 | 0 | ||
10 | 48 | 27 | 0 | 52 | 440 | 0 | 10 | 62 | 320 | 3 | 49 | 515 | 0 | ||
11 | 62 | 616 | 0 | 53 | 617 | 0 | 11 | 71 | 530 | 0 | 50 | 636 | 0 | ||
12 | 34 | 19 | 0 | 53 | 629 | 0 | 12 | 69 | 525 | 0 | 50 | 699 | 0 |
Table 2. Comparison of operating data before and after maintenance