Elbow Pipe Optimization for Power Plant
Application
Industry: Coal-Fired Power Plant
Capacity: 800MW * 3 units
Country: Taiwan
Problem
The plant constantly experienced pipe leakage in the elbow pipes of fly ash conveying pipelines at Economizer (ECO), Air Pre-Heater (APH), and Selective Catalytic Reactor (SCR) every 4 to 6 months. The conveying system is positive pressure type, so the leakage was visible and caused contamination in the nearby surroundings. The pipe bore is 5” (ID=100mm) with chrome alloy liner and R500mm curve radius. The pipes had been patched with concrete whenever leakage was observed, but obviously such solution has been proven to be futile.
Solution
Pipe leakage caused by erosive wear is a common pestering problem, which has a lot to do with particle velocity and hardness, solids loading ratio, and particle impact angle. These three parameters are subjected to the more complicated conditions of plant process and ash conveying system throughput design, thus, the simpler way to better withstand erosive wear is to improve the particle impact angle and pipe hardness.
Tai & Chyun recommended the plant to replace the original elbow pipe with inner ceramic-lined sleeve longer radius elbow pipe. By increasing the bend radius, the bend to pipe diameter ratio (D/d) is also increased, whereas the particle impact angle is decreased, and thus the erosive wear is kept to the minimum. The hardness of ceramic liner is 10 MOHS, which is higher than that of chrome alloy liner, 5 MOHS. The increased hardness of pipe liner material allows longer lifetime for the elbow pipe.
Original Elbow Pipe | Tai & Chyun Elbow Pipe | |
Bend to pipe diameter ratio (D/d) | 500/100 | 1000/100 |
Liner material | Chrome alloy | Ceramic |
Liner hardness (MOHS) | 5 | 10 |
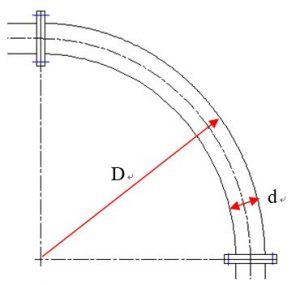
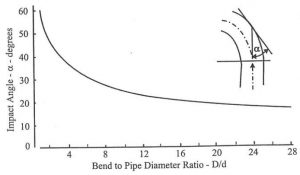
*Influence of bend geometry on particle impact angle – David Mills, 2016, Pneumatic Conveying Design Guide
Benefit
Initial trial with Tai & Chyun ceramic elbow pipe was carried out in unit 2. After running for one year, no leakage was found and satisfactory achieved. Therefore, customer continued to adopt Tai & Chyun elbow pipe in unit 1. Sixteen sets (more than 30 elbow pipes) had been replaced with addition of 500mm ceramic straight pipe at the outlet of each ceramic elbow pipe to further reduce the risk of pipe leakage. Up until now, the pipes installed in unit 2 earlier in 2019 are still in good condition that maintenance or patching is no longer necessary.
Picture
Before
After
To ECO/SCR ash silo
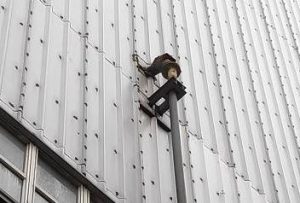
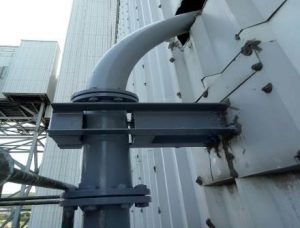
SCR ash pipe
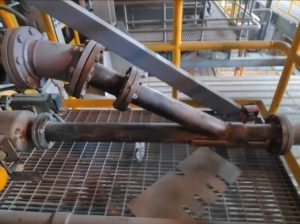
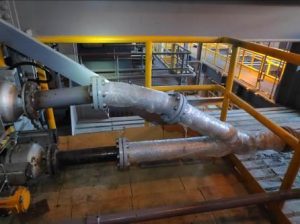
APH ash pipe
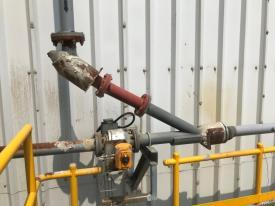
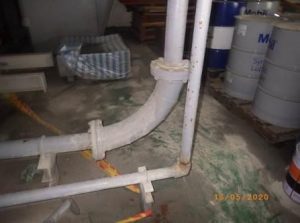
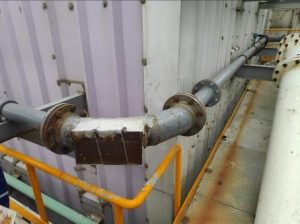
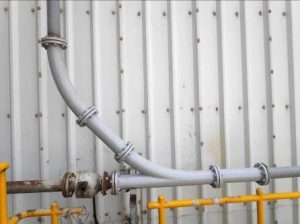
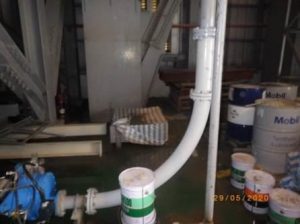
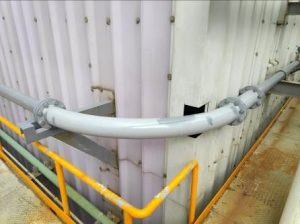
ECO/SCR/APH ash pipe to silo
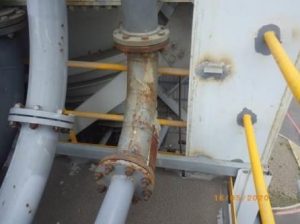
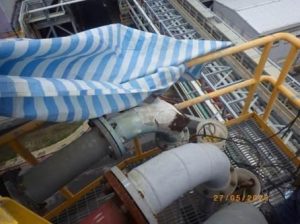
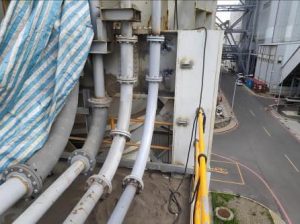
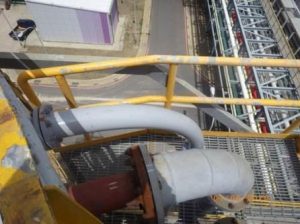