Ash Handling System Rehabilitation – Dense Phase
Application
Industry: Power, 25 MW x 2 units
Process: ESP fly ash handling system
Country: Indonesia
Year of Commissioning: 2019
Period of Project Execution: July-August, 2024
Problem
The plant’s existing design of ESP fly ash handling system is dense phase type. There are six ESP hoppers, thus six blow tanks in each unit. The PLC (Programmable Logic Controller) has lost connection with the local equipment, so user had to operate the system manually using local control panel. Furthermore, fluidizing disc of the blow tank was found blocked and ash was clogged inside the blow tank due to high moisture in the conveying air from air compressor. As an immediate solution, ash had to be drained onto the ground and cleaned by labor. The filter bag on silo top was also found clogged so ash was forced out from relief valve. There were also issues with silo unloading system such as broken dry / wet unloaders, silo fluidizing blower and heater not functioning properly.
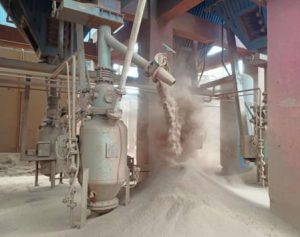
Ash being drained onto the ground due to ash handling system malfunctioned
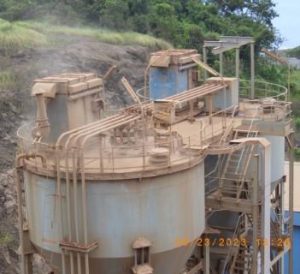
Filter bag clogged and missing fan
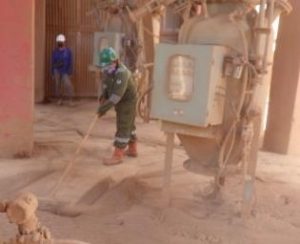
Ash being cleaned by labor
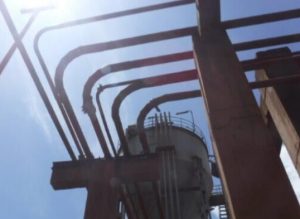
Mitered elbow pipe leakage
Solution
Aiming to restore the ash handling system to full functional, Tai & Chyun planned the work scope, parts supply, and installation supervision as below.
1.Replace PLC & SCADA:
Integration of existing and new equipment was carefully executed to ensure complete control of the system, from ash transporting to silo unloading. Control cables and instrument air tubes were also replaced. The condition of MCC room, where PLC panel is located, was also improved by adding extra air conditioning.
2.Replace blow tanks, valves, instrument & local control panels:
Wear-resistant valves and Rotating (Double) Disc Valve with tungsten alloy disc were installed as inlet, discharge and vent valves. Level switch was replaced from capacitance type to fork type to allow accurate signal. Local control panel and pressure transmitter were also replaced.
3.Replace filter bag and dry unloader:
Existing broken filter bag and dry unloader were replaced with new ones.
4.Maintenance:
Repair / maintenance was conducted on the air compressor, silo fluidizing blower and heater, silo unloading diverter valve, and wet unloader motor. Silo fluidizing pad was cleaned. All necessary works were done to ensure the smooth transportation of ash from ESP hopper to silo, and finally to the unloading truck.
Conclusion
The project took around 25 days for each unit. Some works were executed while a unit was still under operation and some tie-in works were completed during shutdown. After rehabilitation, ash can be conveyed smoothly and automatically to the silo. The plant no longer has to drain the ash onto the ground and clean it manually. Together with ESP maintenance, less emission from the stack is achieved and the surrounding is ash-free clean.
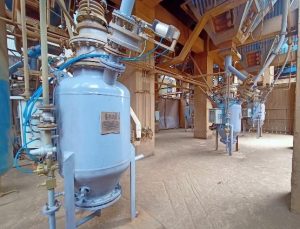
New blow tank with complete accessories
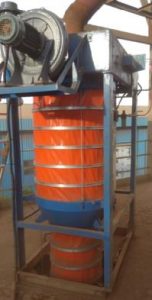
New dry unloader with filter bag
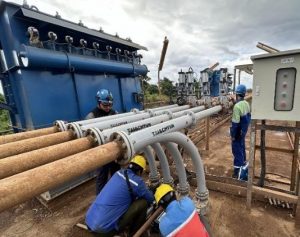
New filter bag & ceramic sleeve pipes
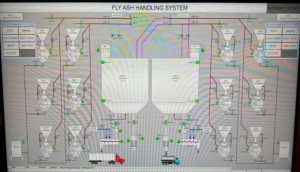
New SCADA system