Fly Ash Pipeline Blockage: Cause & Solution
Pipeline blockages and conveying issues in fly ash systems can be the most frustrating problems encountered in system operation. While various factors can contribute to these problems, they typically stem from either system components or material-related issues. Here are the key areas to monitor and their solutions for dense phase system.
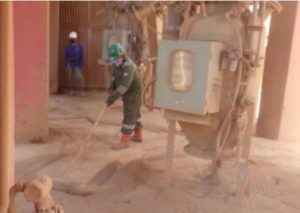
No Ash Flow from Hopper
This condition can result either from arching (also known as bridging) or ratholing. Inspect the casing and insulation of ESP for any leakage, and check the condition of fluidizing pads. Installation of hopper heater or sonic horn helps ease ash flow into the blow tanks.
Air Compressor and Air Supply Lines
Successful ash conveyance requires sufficient air velocity (air volume) and pressure, and quality of air to be clean and dry. Make sure there is enough pressure at air tank, and auto-drain valve should be installed. Check the air filter and regulators along the air supply lines. Make sure there is enough pressure for every conveying cycle, and the pressure restore time between each cycle, for it can affect the total conveying cycle time.
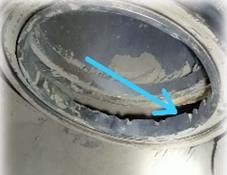
Blow Tank and Valves
Leakage at valves (or passing, not fully closed) is the most common problem in the ash handling system. It can lead to pressure loss during blow tank pressurizing and conveying. Blinding of a fluidizing membrane will also add to the pressure drop across a blow tank. Both conditions result in less pressure available for ash conveying in the pipeline. It means decrease in total conveying capacity and can possibly lead to pipeline blockage. The actual performance of a blow tank can be monitored easily via conveying pressure trend when a pressure transmitter is installed on the air supply line.
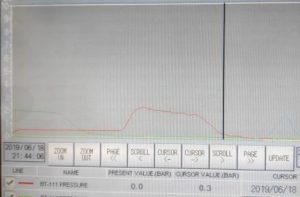
Normal Conveying Pressure Trend
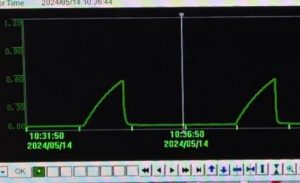
Conveying Pressure Trend with Blinded Fluidizing Membrane
If the conveying system is only controlled based on time, instead of level switch and pressure transmitter, the set time for filling and conveying should be carefully adjusted according to different ash condition. Excessive filling time can make blow tank clogged and insufficient time for conveying can lead to pipeline blockage.
Pipeline
Pipeline itself is seldom the root cause for pipeline blockage. However, a gradual reduction in the system output over a period of time is likely to be due to ash build-up in the pipeline. If the pipeline is not purged after every conveying cycle, after some time, there may be sufficient ash left in the pipeline to cause blockage of the line. In the case of all blow tanks connected in only one pipeline for one ESP, the whole system has to be stopped during a valve repair job. Therefore, it is recommended to have independent discharge valves for each blow tank and install more than two pipelines for one ESP.
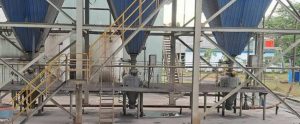
Silo and Vent Filter
If ash comes out from the relief valve on the silo top, it indicates the vent filter is clogging or silo high level. Clogged bag filter can create back pressure and hinders the ash conveyance. Filter bags should be replaced in every shutdown, and enough air pressure for the pulse valve is required for effective cleaning of the filter bags.
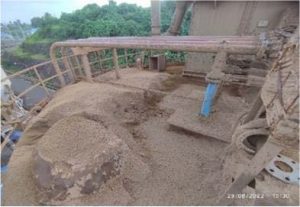
Ash Characteristics & Operation
Fly ash collected at economizer and air pre-heater hopper is coarse ash with big particle size, with mean particle size of 100µm, while ash collected at ESP/Bag house is fine fly ash with mean particle size of 25µm. Coarse ash has poor air retention and thus should be conveyed via bottom-discharge blow tanks. The capacity of ash handling system is usually designed with the tolerance more than 50%. If change of coal leads to pipeline blockage, while all equipment is in good condition, then an upgrade for system capacity should be considered.
Best Practice for Preventing Pipeline Blockage
- Regular system monitoring and maintenance
- Proper pressure management throughout the system
- Close attention to valve operation and timing
- Regular cleaning and inspection of critical components
Reference:
- D. Mills and V.K. Agarwal, Pneumatic Conveying Systems, 2nd ed., 2009.
- EPRI, Ash Handling System Maintenance Guide, 2005.
- 3.Qi, L.C, Coal-Fired Power Plant Ash Handling System and Control Technology, 2014