ESP Retrofit with High Frequency Transformer Rectifier Upgrade in Petrochemical Plant
Application
Industry : Petrochemical
ESP OEM : Hitachi
Process : Power Boiler
Country : Thailand
Problem
A Power Boiler ESP with capacity of 54 MW in a petrochemical plant in Thailand had been undergone periodical maintenance, however, its performance had been inevitably deteriorated since it had been operating for 27 years. The ESP operation was unable to run at its full rating of T/R set. The emission during operation was 288 mg/Nm3 based on its emission designation of 300 mg/Nm3. The end users expected to bring back ESP performance and improve collecting efficiency even beyond its capacity.
Designated Emission | Operation Emission | Targeted Emission |
300 mg/Nm3 | 288 mg/Nm3 | Below 150 mg/Nm3 |
Table 1: Emission rate among ESP design, operation and target
Solution
Tai & Chyun has been awarded for this ESP retrofit project. We provided all-in-one service from design, manufacture, installation as well as commissioning. The project included dismantlement of the entire internal parts inside the ESP and reinstallation of new parts with a 45-day on-site installation and supervision service. Major ESP parts such as Collecting Electrode (CE), Discharge Electrode (DE), and Transformer Rectifier (T/R) Set, including Access Door were retrofitted into new designs as shown in Table 2.
Old Design | New Design | |
Collecting Electrode (CE) | 575mm width | 7 pcs per row | 480mm width | 8 pcs per row |
Discharge Electrode (DE) | 21 Barbed-type DEs per layer | 8 RDEs per layer |
Power Supply | Conventional T/R set for all fields
Input: 380V/50Hz Output: 65kV/500mA |
HFTR for 1st & 2nd field
Input: 400V Output: 83kV/675mA |
Conventional T/R set for 3rd field
Input: 380V Output: 72kV/700mA |
||
Access Door | Single | Double |
Table 2: Comparison between old and new design
The width of CE has been reduced with increased number of CEs per row against its original design. This change has no effect on the Specific Collecting Area (SCA), but it benefits the ease of maintenance due to less reduction area when bent or deteriorated CE is required to be cut off. Old DE has been replaced with new Rigid Discharge Electrode (RDE) that resulted in reduced number of DEs after retrofit to 80% while corona generation is even more efficient than the original design, which increases ESP performance and also benefits future maintenance respectively.
Along with major parts, other related mechanical parts such as rapping system, Gas Distribution (GD) screen, inlet/outlet expansion joint, etc. have also been renewed. Single Access Door has been upgraded to Double Access Door in order to eliminate the possibility of air leakage through the door and avoid moisture from building up inside the ESP.
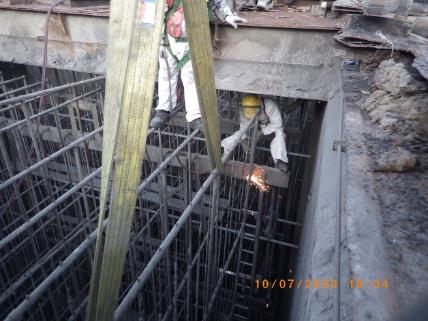
Dismantling the entire internal parts
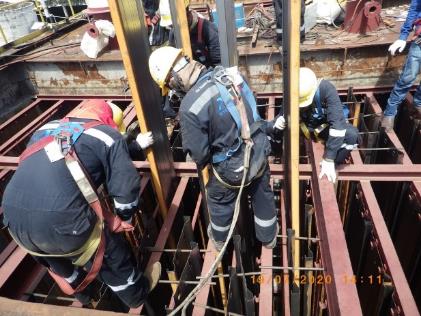
Installing new CE
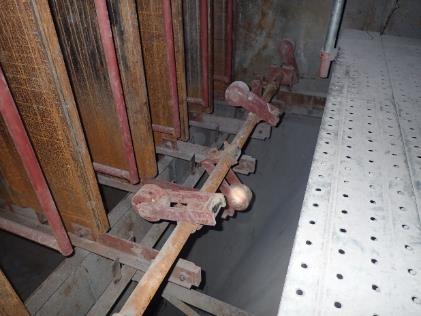
Installed DE/CE rapping system
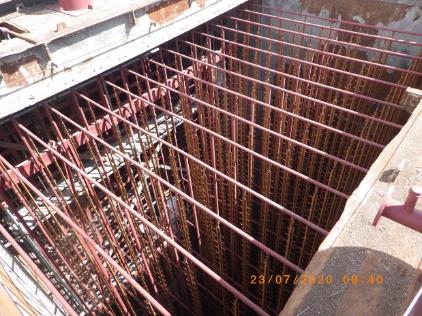
Newly installed RDE
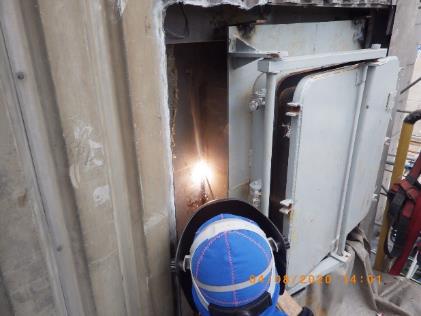
Installing Double Access Door
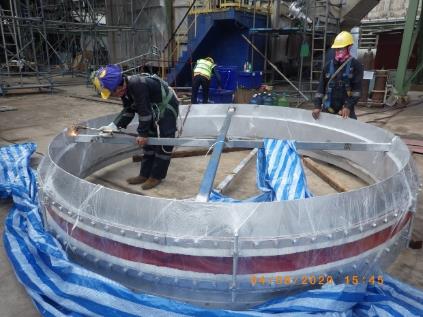
Installing inlet/outlet expansion joint
In electrical aspect, 2 sets of High Frequency Transformer Rectifier (HFTR) have been replaced in the 1st and 2nd field while another new conventional T/R set has been installed in the 3rd field. HFTR produces higher average voltage than conventional T/R, generating higher migration velocity that leads to higher ESP collecting efficiency.
Furthermore, a new control panel with Graphic Display Unit (GDU) keypad has been installed. An interlock key system provides Lock Out Tag Out (LOTO) procedure for safety concern during operation and maintenance.
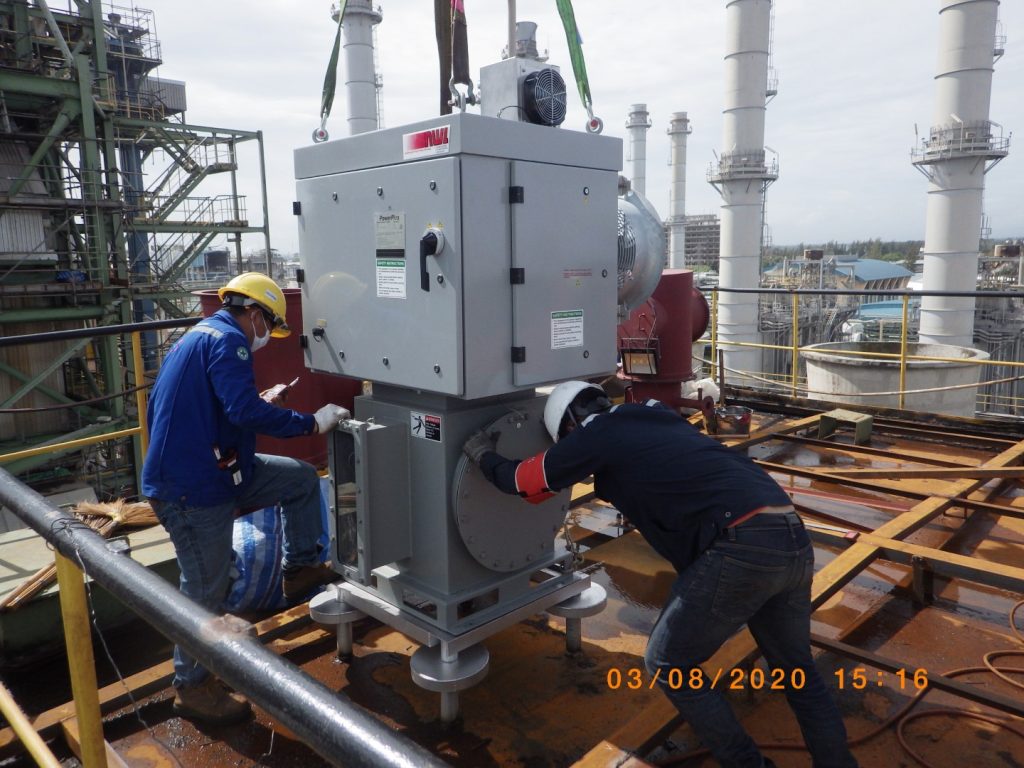
High Frequency Transfomer Rectifier Upgrade
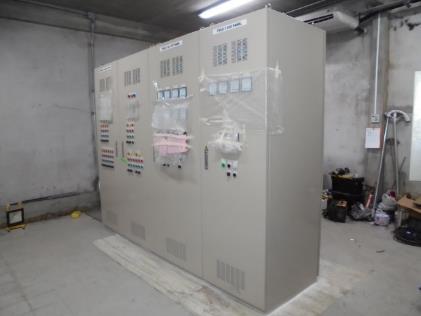
Control Panel Installation
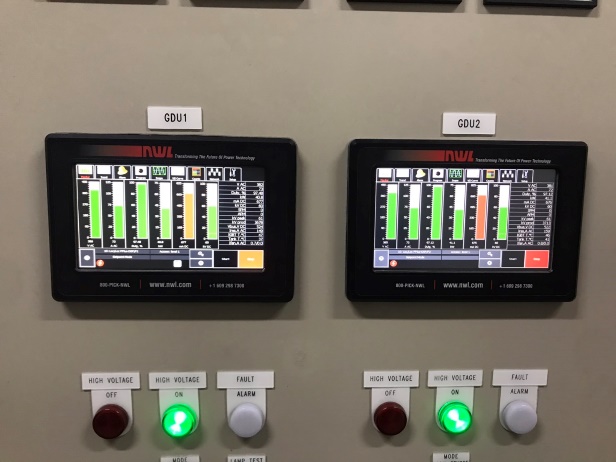
Newly installed GDU keypad
Benefit
The new design of CE and RDE together with HFTR upgrade enable the ESP to increase its dust collecting efficiency more than its original designation while also beneficial to future maintenance.
As a result, the particulate emission at the ESP outlet has been significantly reduced from 288 mg/Nm3 to 108 mg/Nm3 and ESP efficiency has been increased from 87.98% to 98.51%. Moreover, this remarkable result of the performance test has been achieved even with much higher dust load from the ESP inlet.
Inlet Particulate (mg/Nm3) @ 7% O2 | Outlet Particulate (mg/Nm3) @ 7% O2 | ESP Efficiency (%) | |
Before Rehabilitation | 2,396 | 288 | 87.98 |
After Rehabilitation | 7,301 | 108 | 98.51 |