Application
Kiln Upgrade of a Malaysian Cement Plant.
Problem
- Dust emission efficiency exceeds the permitted emission values set by the local regulating authority. Poor efficiency was caused by the increase in gas volume of the ESP due to upgrade of production capacity by an additional 37.5%.
- Project Difficulties: Designing the additional surface collecting area of the current ESP; Connection of the new ESP field to the current ESP; Construction of steel and cement platform for the foundation of the new ESP field; Language Barrier due to the 4 different languages spoken among the engineers and workers.
- Cultural differences, since the lead contractor is an engineering firm from Thailand, Tai & Chyun is a Taiwanese engineering firm, and the contractor is a local Malaysian construction firm. This required extra time during negotiations and decision-making.
Solution
Increase the surface collecting area by adding a new collecting field to the current ESP within the limited area of the current location of the ESP. With the new field installed, treatment time of the gas volume will increase thereby increasing the ESP’s dust collection efficiency. General Arrangement Drawing:
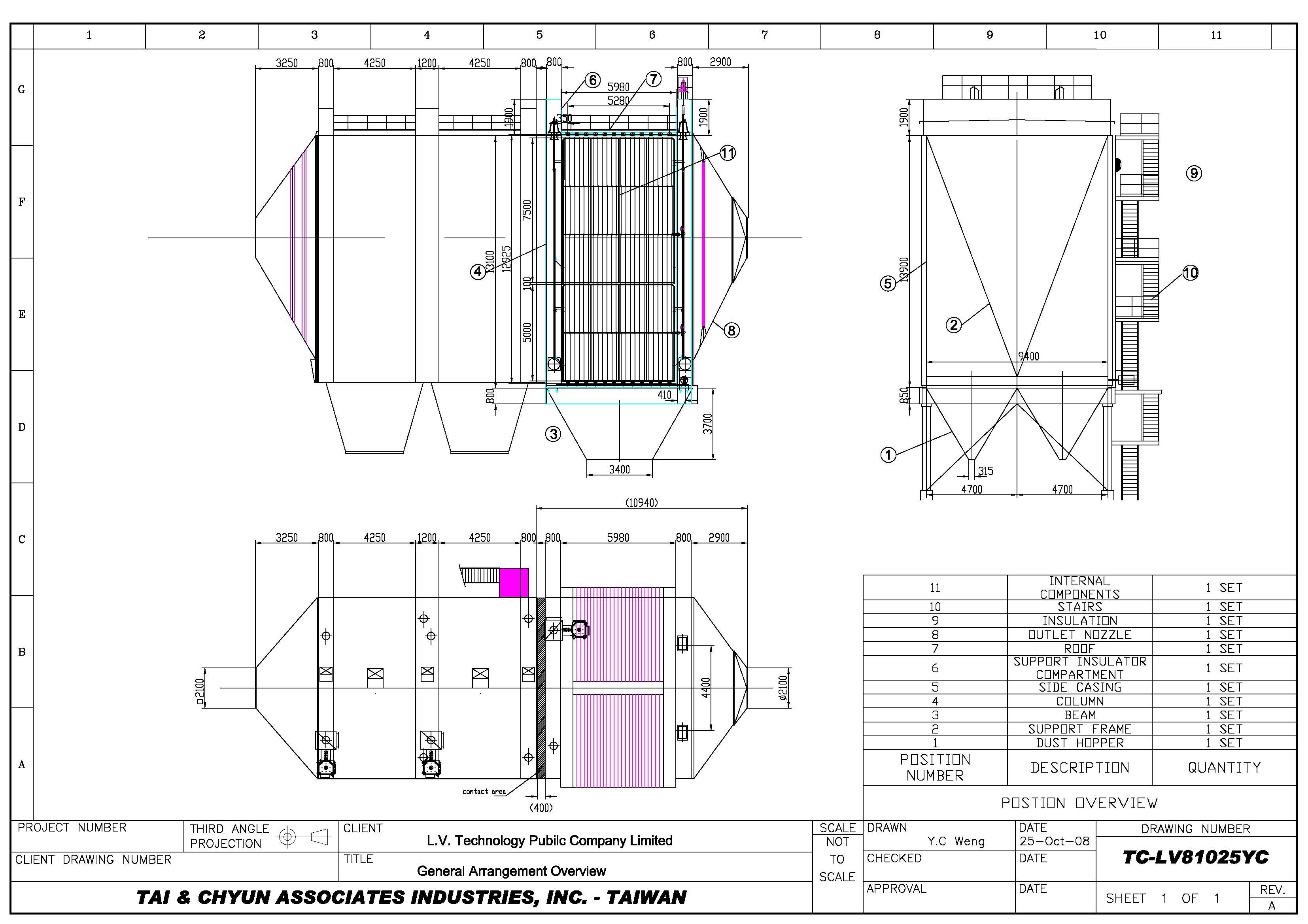
Benefit
Construction of main parts started on September 8, 2009. After shutdown on September 27, 2009, installation of internal components began. Testing was finished on October 12, 2009. The installation was finished in 16 days and was according to schedule.
On October 12, 2009,all required tests were performed by Tai & Chyun Engineer such as open circuit tests, air load tests, and dust load tests. V-I Curve during air load test showed a maximum of 70 kV / 2000 mA, verifying that the design has reached the required standards. Since commissioning up to present, the ESP has operated smoothly. ESP efficiency before and after upgrade:
Original Design | New Design | |
Gas Volume (Nm3/min) | 2,300 | 2,717 |
Operating Temp.(℃) | 230 | 280 |
Collection Efficiency(%) | 15g/Nm3→0.1g/Nm3
(99.33%) |
0.05g/Nm3
(99.66%) |
ESP outer appearance | ![]() |
![]() |