Application
RM1 ESP & RM 2 ESP of a cement plant located in West Malaysia.
Problem
- There was excessive dust emission of around 250 mg/Nm3. The customer wants to rehabilitate the ESP to ensure that the final dust emission through the exhaust chimney is less than 50 mg/Nm3.
- ESP had been in operation for more than forty years, and some of the internal parts have reached the end of their working life
- The TR sets were not capable of maximizing the performance of the ESP
Solution
Tai & Chyun was invited to inspect the ESP and provide solutions in lowering the emission. Few options were provided, and it was finally decided to rehabilitate the internal parts of the ESP to new design and also replace the old TR sets with new ones. The rehabilitation works were completed in four (4) weeks. The scope is detailed below:
- Installation of New CP & CP Suspension Beam, DE & DE Suspension Frame and Rapping System
- Installation of New TR sets
- Replacement of GD Screen & Support Insulators
- Cleaning of Screw Conveyor
The difficulties encountered during the rehabilitation work were the bending of DE which was found due to installation process. It was corrected using the F spanner. More seriously bent DE was corrected with heat treatment.
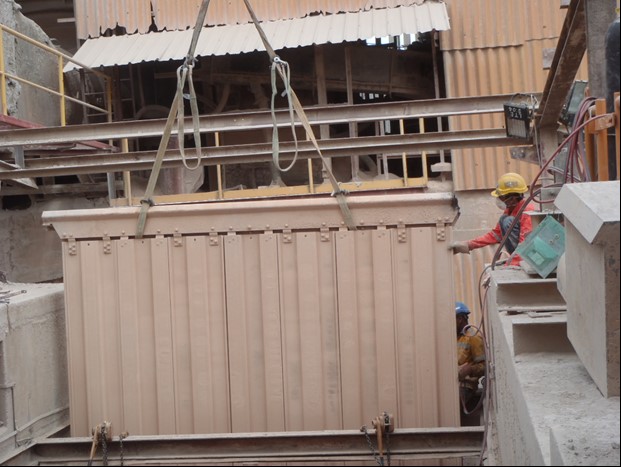
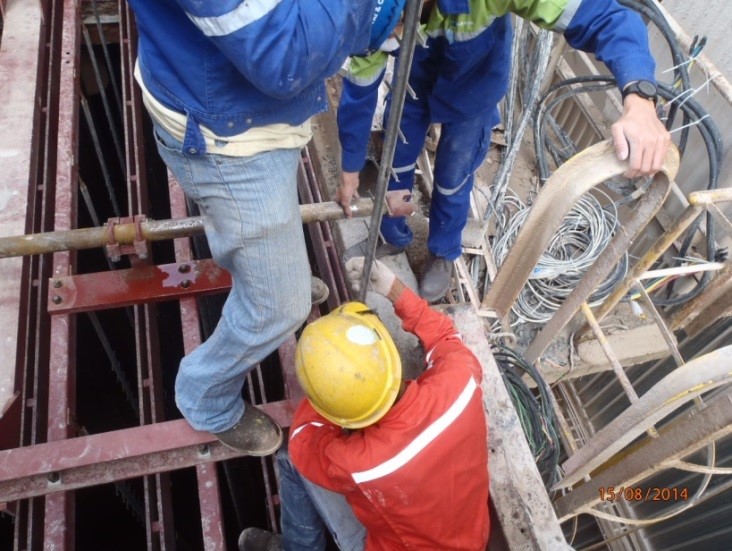
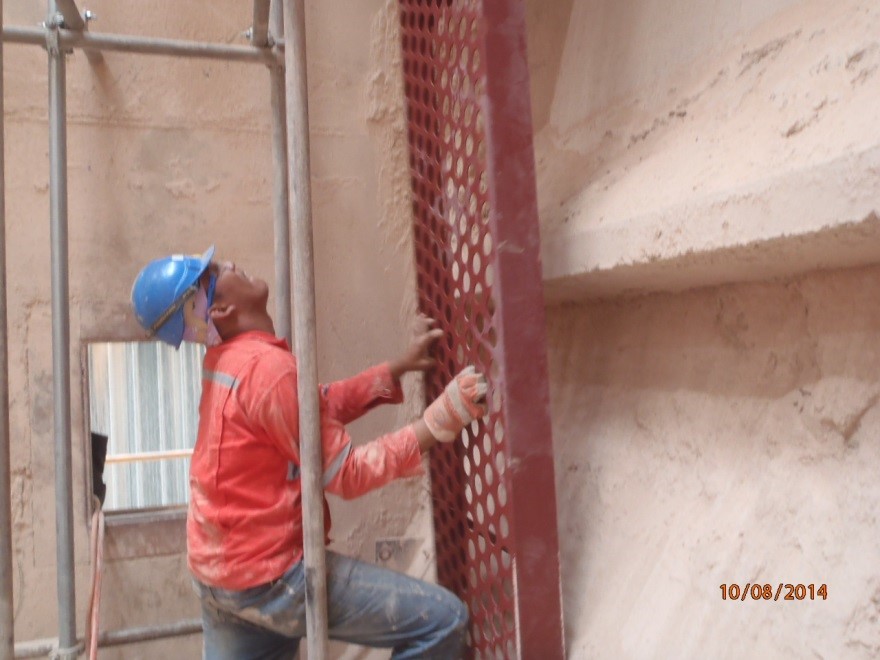
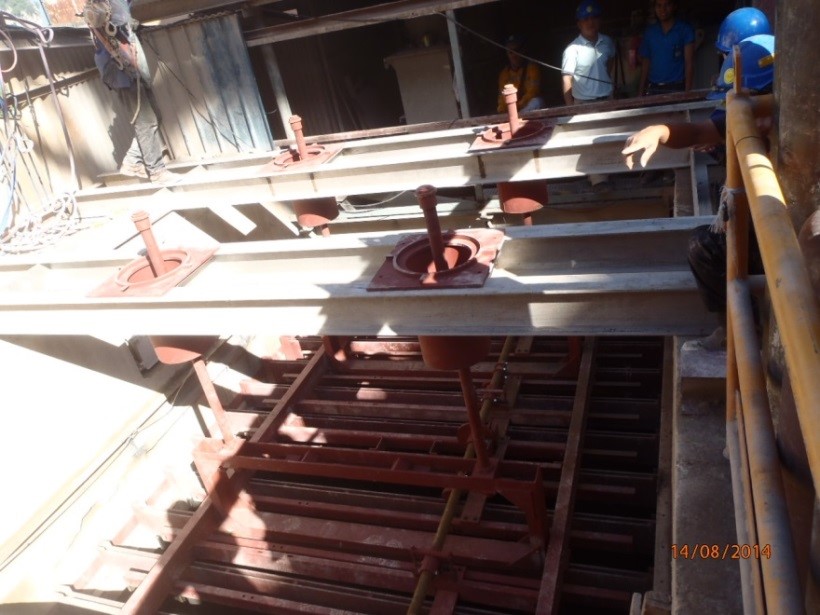
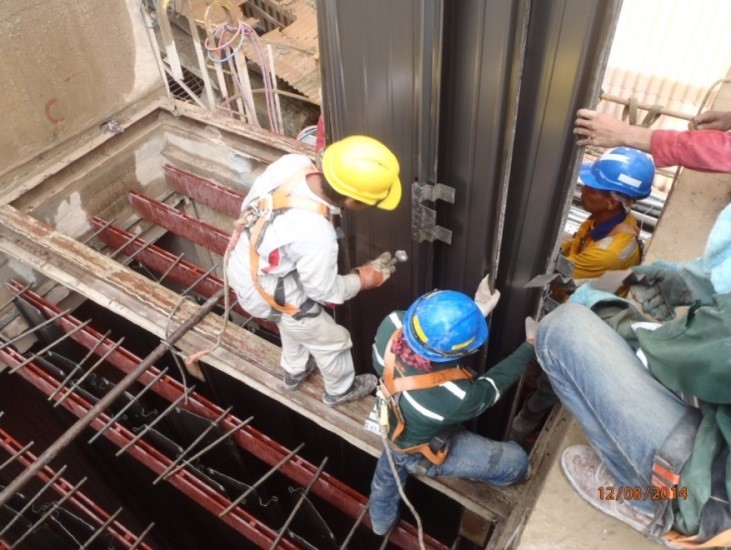
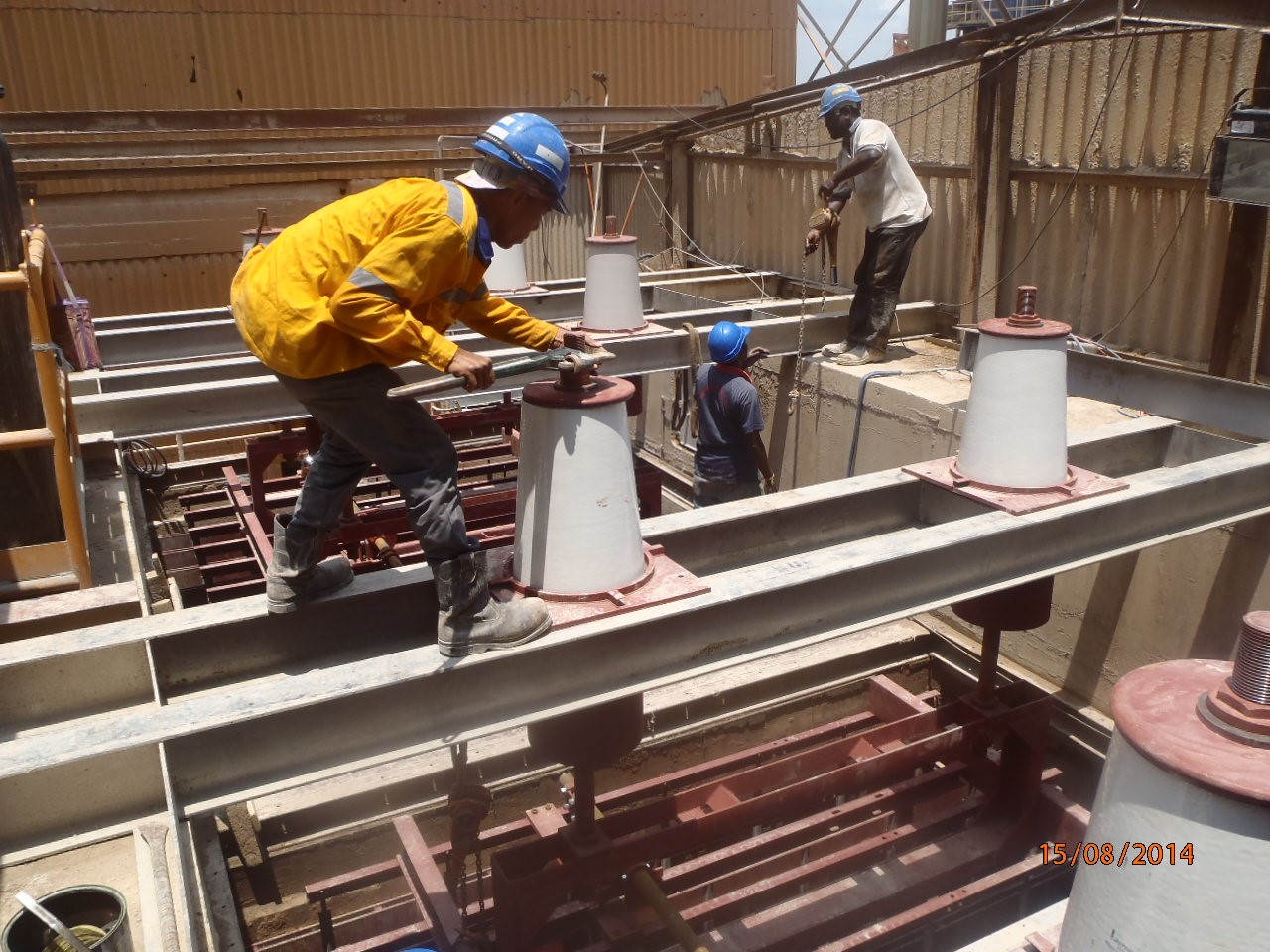
Benefits
Dust Emission after rehabilitation becomes stable and satisfactorily reached the customer’s expectation.
ESP | Before | After |
RM1 | 204mg/Nm3 | 50mg/Nm3 |
RM2 | 241mg/Nm3 | 59mg/Nm3 |
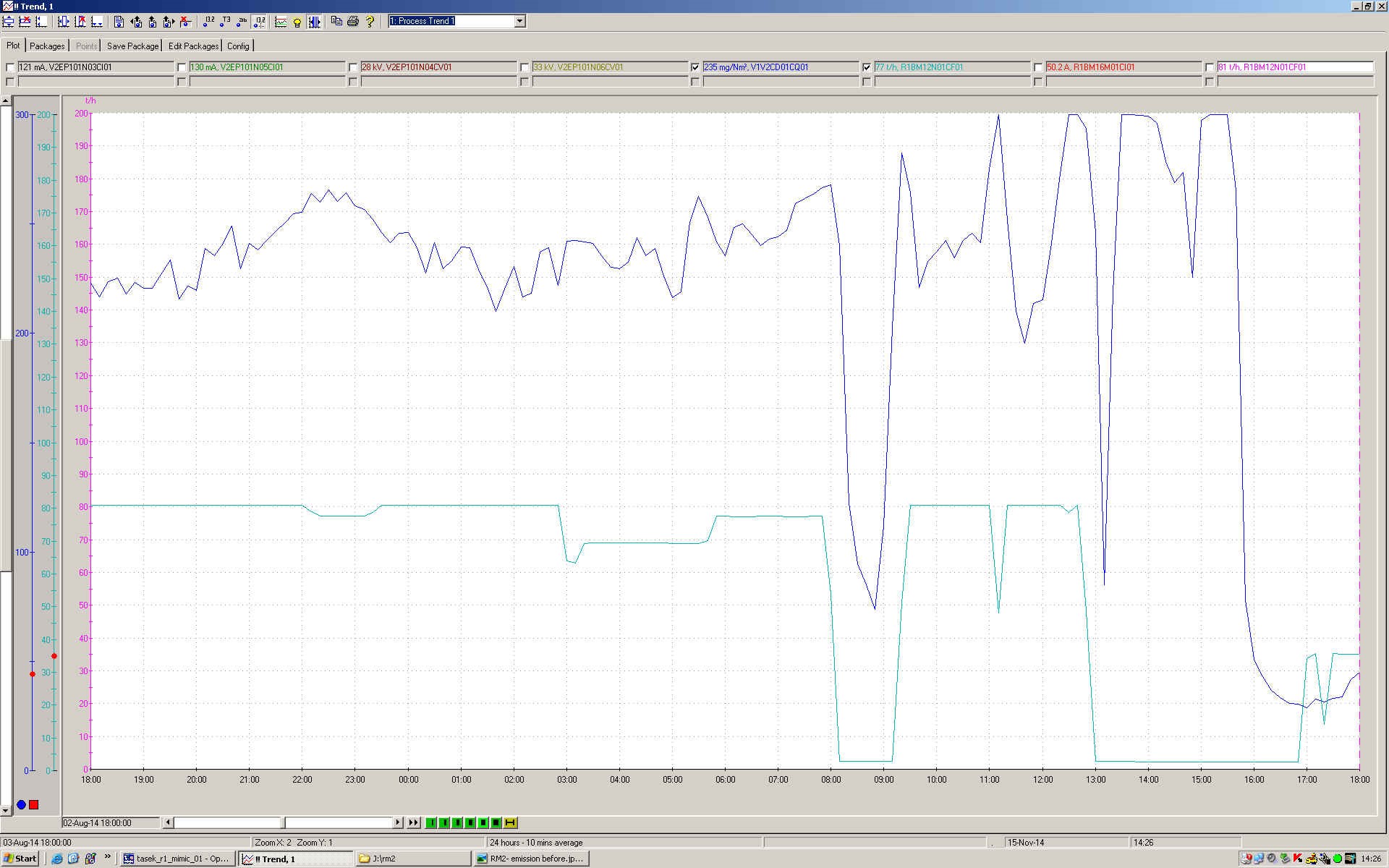
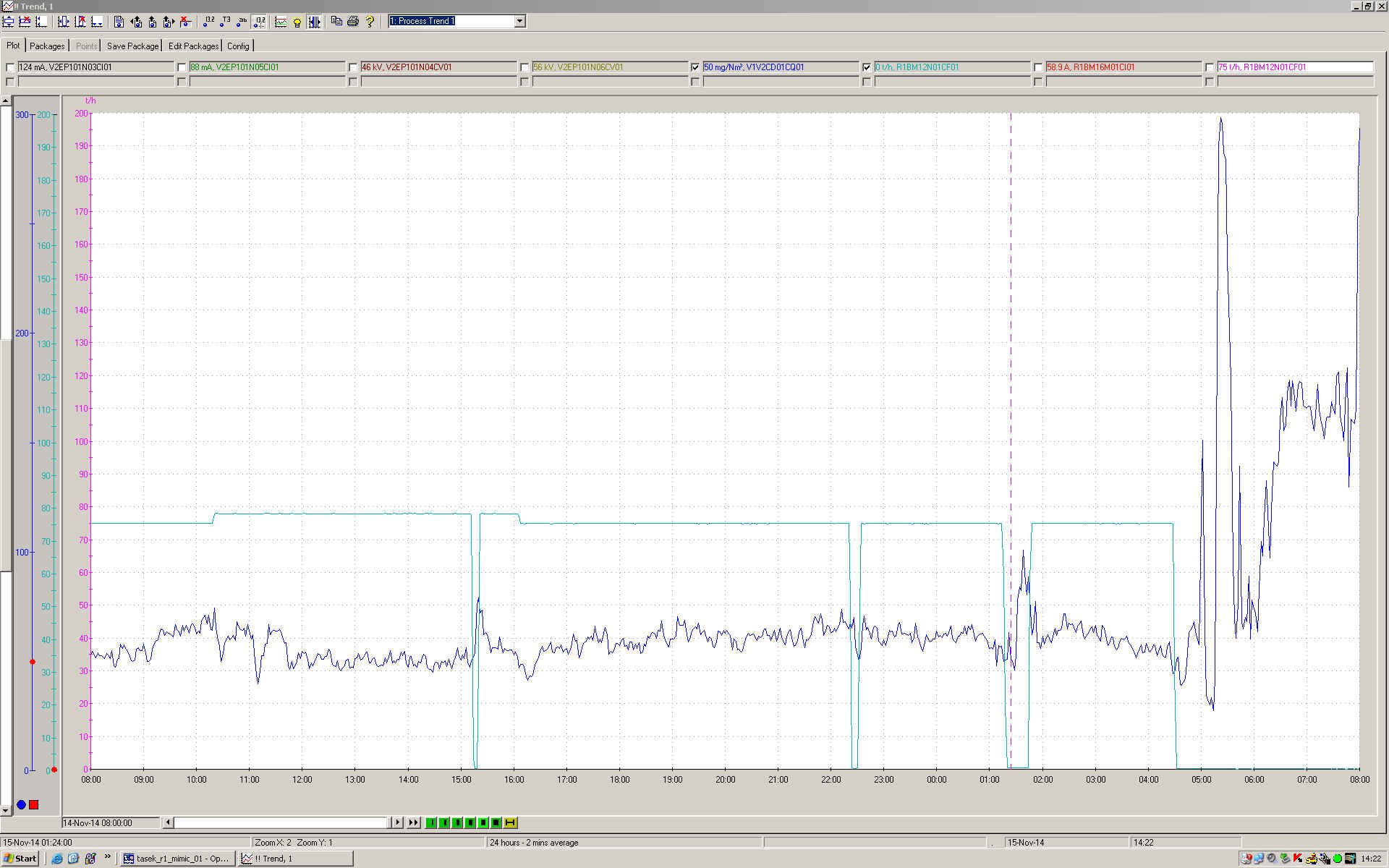
RM1- Before (left) & After (right) [*dark blue line indicates trends of emission]
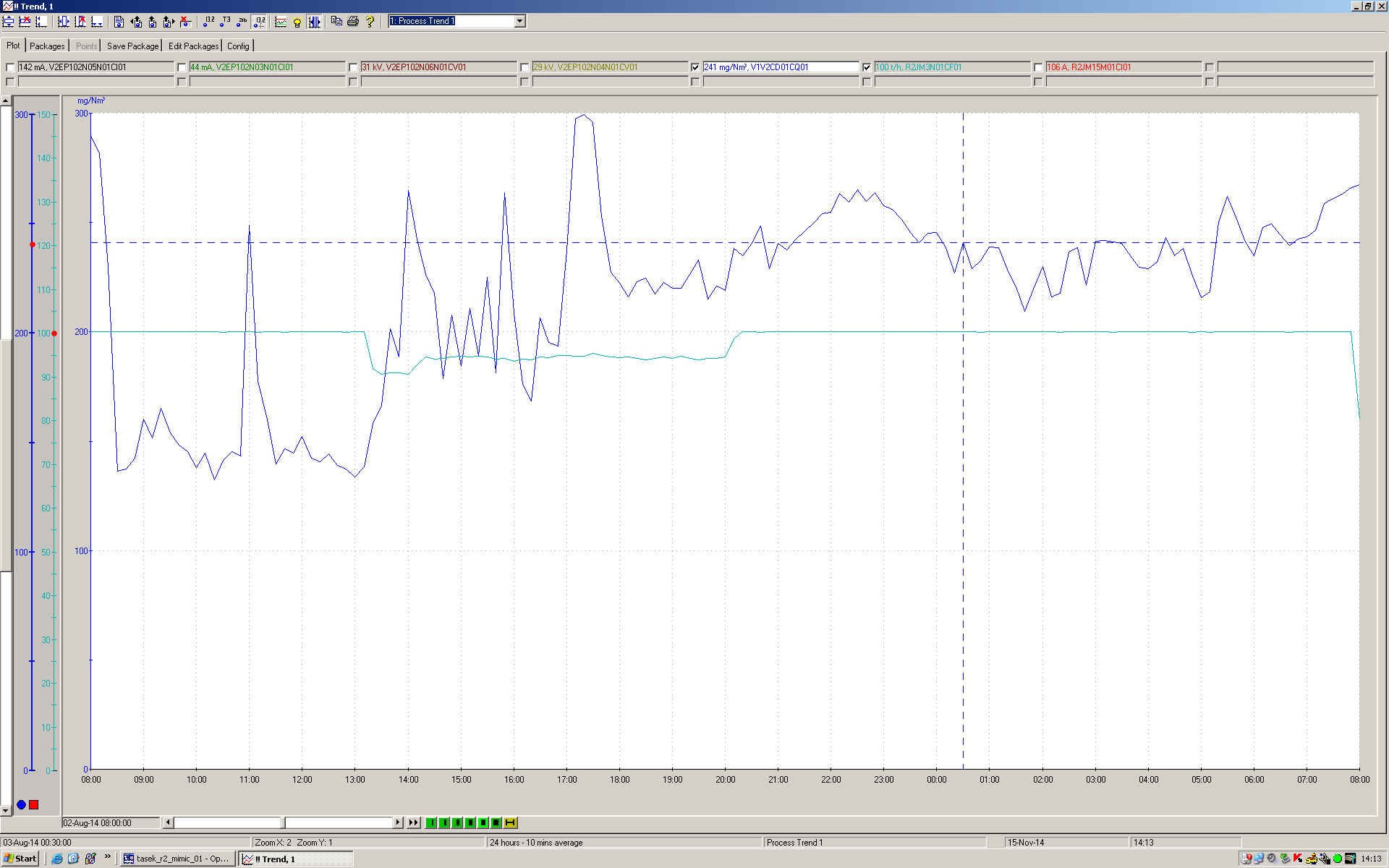
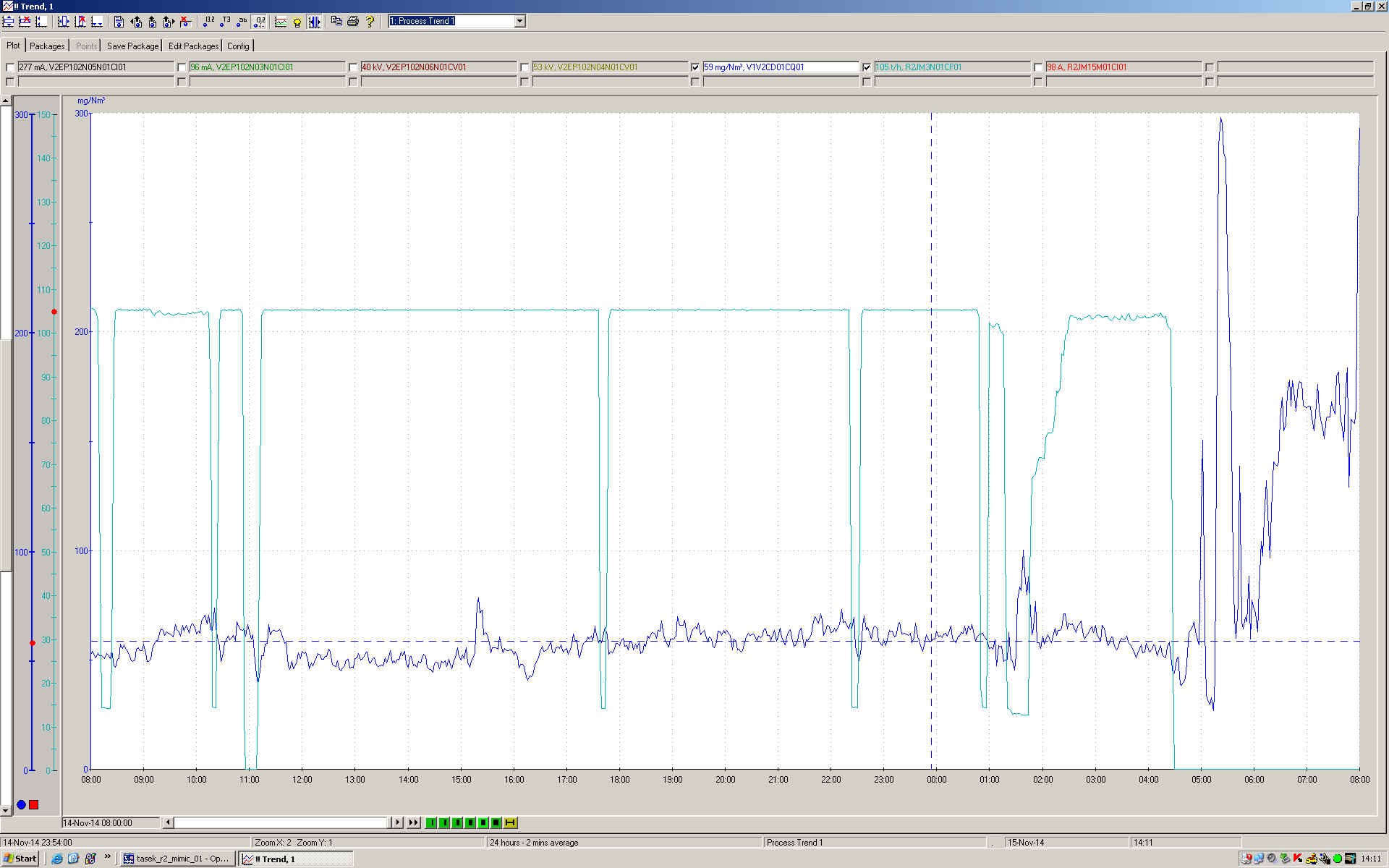
RM2- Before (left) & After (right) [*dark blue line indicates trends of emission]
Field Number | Before | After (No Load) |
RM1 Field 1 | 37kV/147mA | 40.5kV/370mA |
RM1 Field 2 | 54kV/112mA | 56.0kV/360mA |
RM2 Field 1 | 34kV/129mA | 46.0kV/370mA |
RM2 Field 2 | 34kV/98mA | 41.0kV/360mA |
Tai & Chyun is always ready to provide the modern way of enhancing precipitator performance and all the parts needed in ESP with good after sales service.