Application
Coal-fired boiler ESP in Indonesia.
Problem
The mechanical parts inside ESP have never been replaced for more than 25 years. Therefore, most of the parts already reached their life span. Moreover, the parts inside were exposed to high temperature from unstable operation. Therefore, there are many mechanical problems inside ESP. Accordingly, below ESP problems were observed during the ESP inspection conducted by Tai& Chyun engineer.
- Bent, Deformed & Welding failure GD Screen
- Leakage from the rooftop near inlet GD screen area
- Bent GD Screen stiffener
- Worn out bearings, anvil & shaft
- Missing hammers
- Hammer Clamp Failure
- Falling-down hopper baffle plate causing hopper full problem
- Bent CP & DE causing close distance between CP and DE which lead to sparking problem and short circuit
- Dust build-up on CP & DE due to rapping failure
- Missing CP & DE
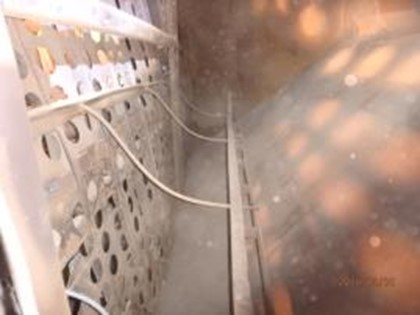
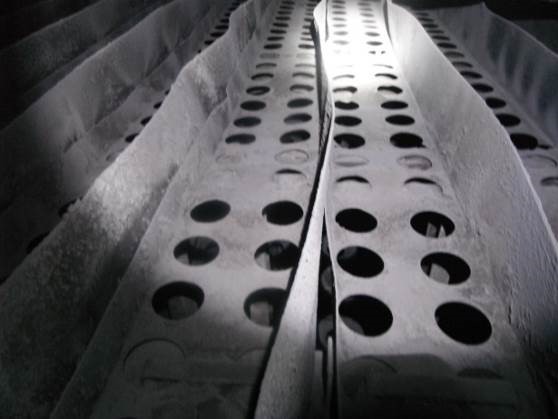
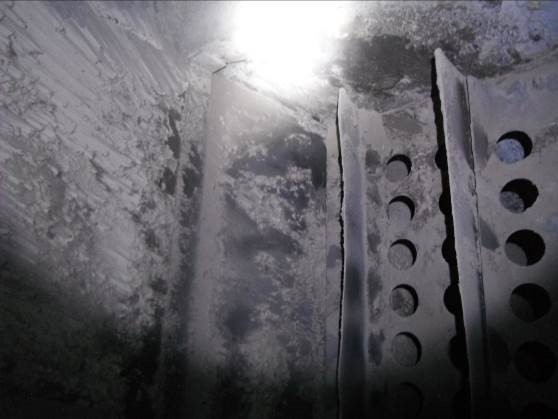

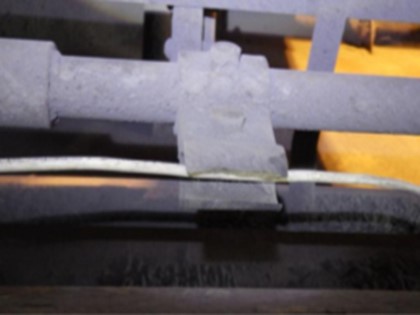
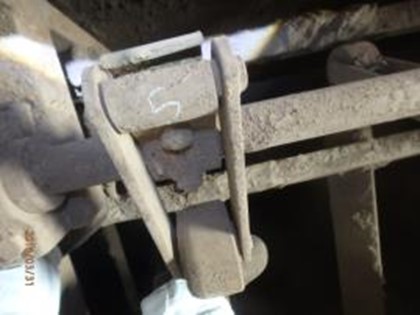
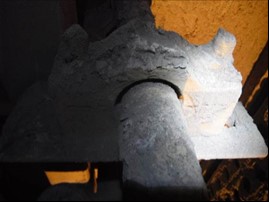
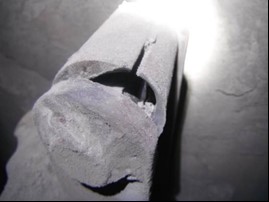
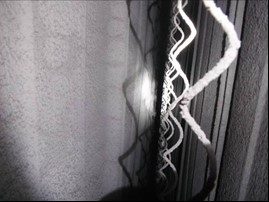
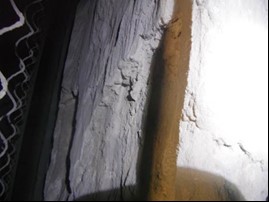
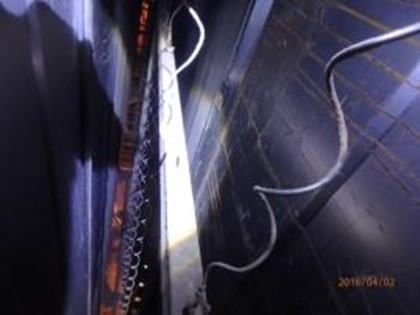
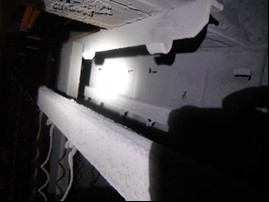
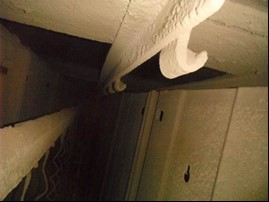
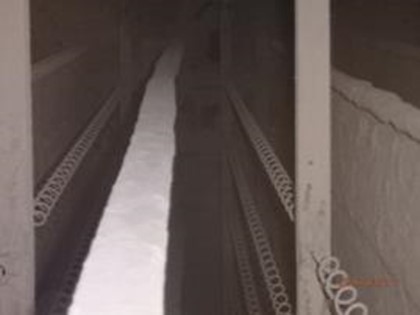
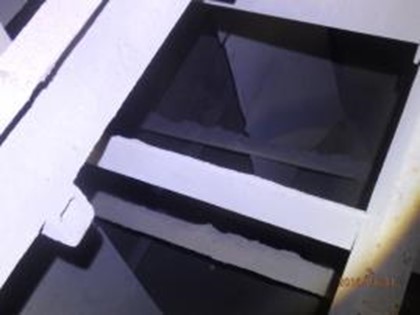
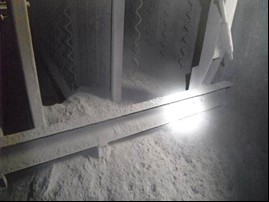
Solution
Tai & Chyun was awarded to supply DE, CP, GD Screen & rapping assemblies, together with supervision. Below are the work scopes which have been implemented in order to improve ESP performance efficiency.
- Replacement of new CP
- Replacement of new Inlet GD Screen.
- Replacement of bearing, anvil, hammer clamp and hammer for CP, DE & GD Screen rapping system.
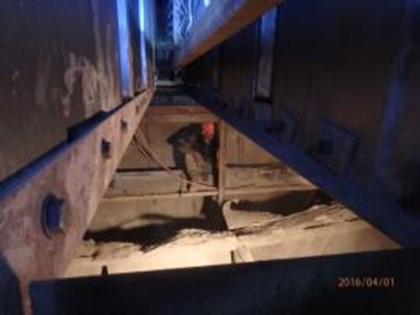
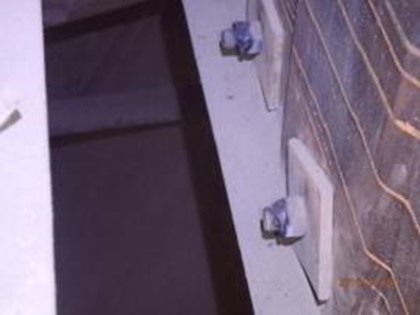
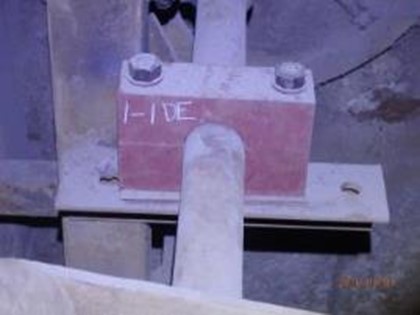
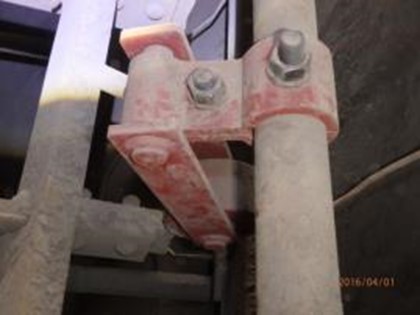
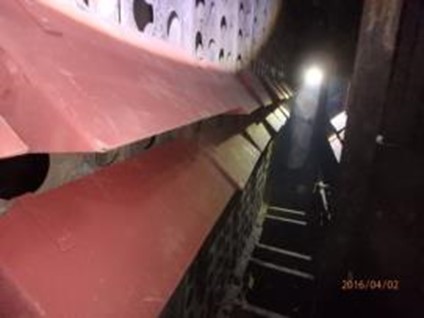
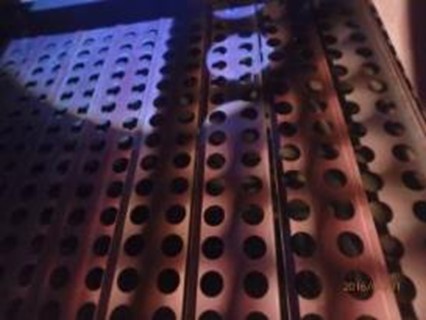
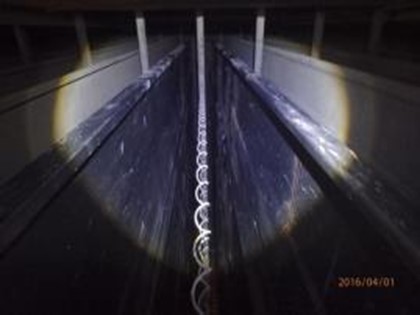
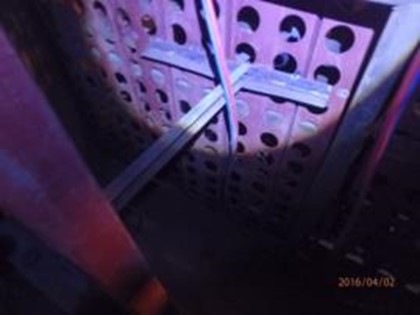
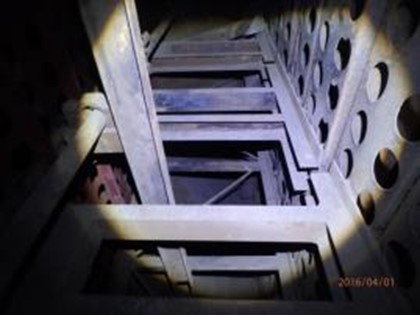
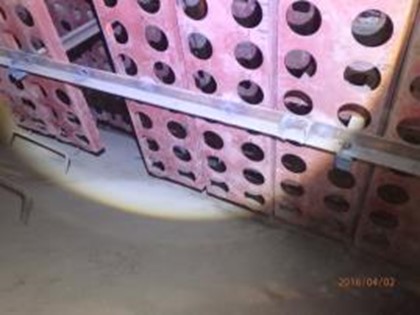
Benefits
After replacement and maintenance of rapping assemblies, rapping efficiency can be improved and it will help solve the problem of falling hammer, which is the main cause of the dust condensation inside the hopper. Also, with new CP & DE replacement, it will solve the problem about close distance between CP and DE preventing sparking and short circuit problem, while replacement of GD screen will also help facilitate the flue gas to be distributed evenly. By renewing the critical damaged parts inside ESP at the minimum downtime, it could ultimately bring the aging ESP back to its original design efficiency. Therefore, it could provide worry-free for the end user regarding ESP issues.