Partial Rigid Discharge Electrode Replacement in a Utility Plant
Application
Industry: Power
Capacity: 1 unit x 500 Megawatts (400MW operating capacity)
ESP OEM / Information:
OEM: Hamon Research Cottrell – 2 Chambers, 6 Fields / Chamber
Start of Operation: 1996
Original Type of Discharge Electrode (DE): Twisted Wire
Rapping Design: MIGI Rapper for both Collecting Plate & Discharge Electrode
Country: Philippines
Problem
The plant has been experiencing dust build-up and breakage of the twisted wire discharge electrode. Severe sparking / arcing and even field tripping due to broken wire DE also occurred, which led to higher level of emission although still within the tolerable limit.
There were several occasions when the plant was required to de-rate the capacity to 200MW in order to look for broken DEs so they could be removed.
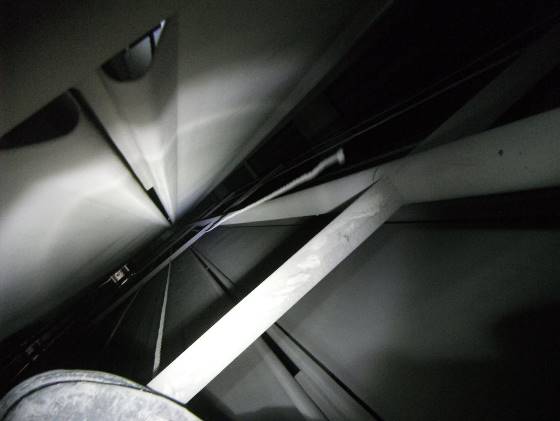
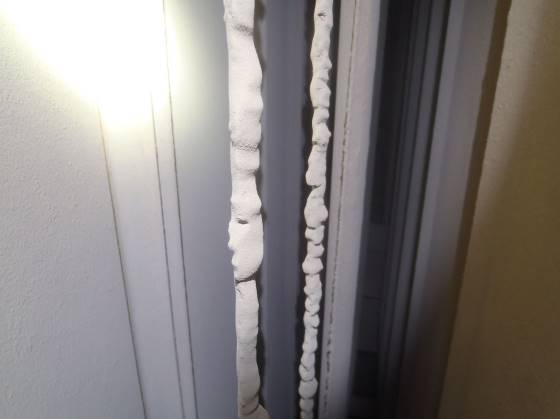
Solution
Tai & Chyun proposed to retrofit the twisted wire DE into Rigid Discharge Electrode (RDE) type without replacing the existing DE frame (rigid frame or strung mast type). First 130 pcs of RDE were trialed to determine the effect on the ESP.
The first partial retrofit into RDE had been carried out at the 1st twisted wires at the upstream of field 1 Bravo Chamber in 2018. End-users noticed better secondary current (mA) with RDE than 100% twisted wire. Succeeding replacement of the 1st and 2nd twisted wires at the upstream and downstream of all the fields were done to achieve result of much better reliability and performance of the ESP.
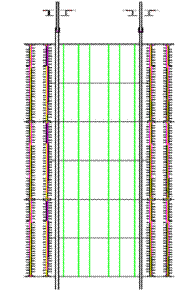
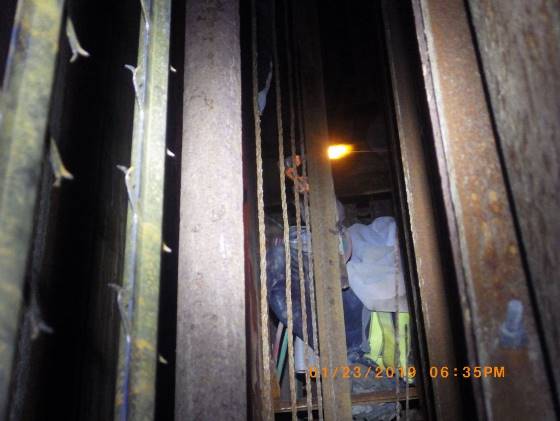
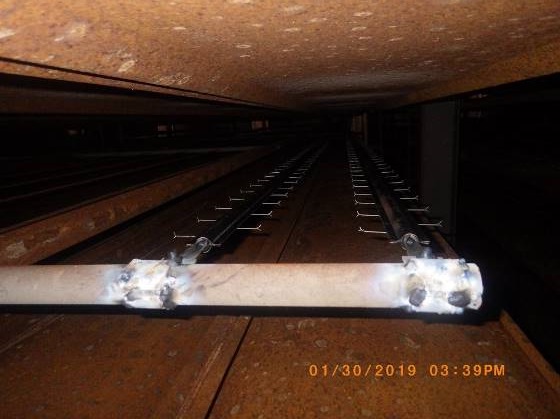
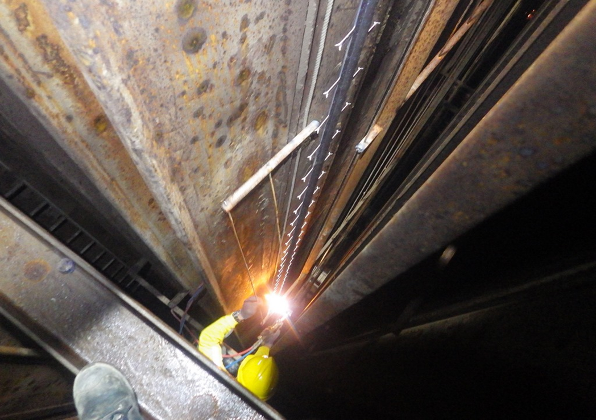
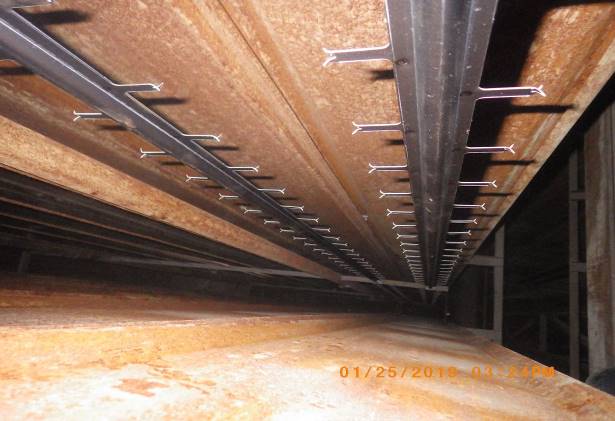
Benefit
After retrofit into RDE at selected locations from fields 1 to 5, each field was capable of operating at high secondary current (mA) values. The T/R sets also reached high secondary current limits without any sparking. It is to be noted that these readings were achieved even without fully replacing the existing twisted wires.
The installed RDEs kept the emission level below regulation limit. Usual mid-year ESP cleaning works could be omitted since the mA were kept at consistent values and did not fluctuate as compared to before.
In return, the plant not only saved on contractor cost but also maximized its profit as production had been running smoothly and continuously with no emission concern.
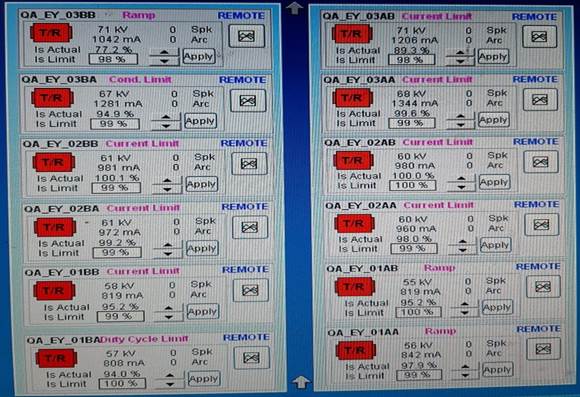