Application
Unit 8 of ESP at Coal Fired Power Plant located in Indonesia
Problem
This power plant has been operating since 2011, using Chinese ESP with capacity of 625 MW. The dust emission from the stack was high at 137mg/Nm3 and the plant received complaints from the residential area nearby, therefore, action must be taken to bring the emission down in order to conform to the governmental standard.
The plant experienced problems and abnormalities of ESP mechanical parts such as CP & DE cracked and detached, missing and damaged rapping part and casing leakage. Internal parts were mostly deteriorated and broken after only 4 years of operation. Furthermore, part drawings were not available from OEM which made it even more difficult for part replacement.
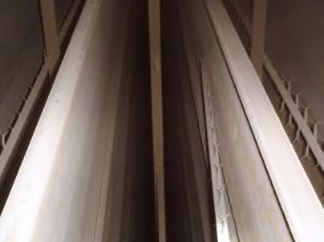
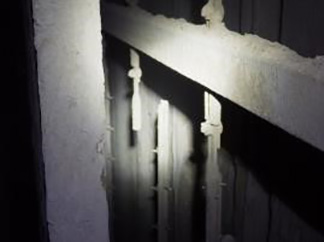
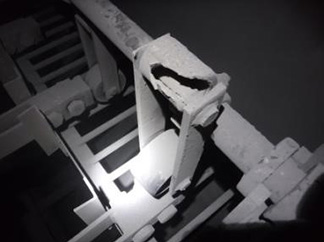
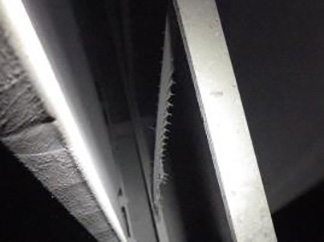
Solution
Prior to the plant approached Tai & Chyun for recommendation in solving their ESP problems, Tai & Chyun had the opportunity to perform an ESP inspection back in 2015 and had come to know and understand the actual ESP condition as well as obtained the measurement of the internal parts. Accordingly, Tai & Chyun proposed the RDE replacement as an initial countermeasure since it’s easy to install and not necessary to open the rooftop. In 2016, Tai & Chyun carried out the RDE replacement for 2 fields.
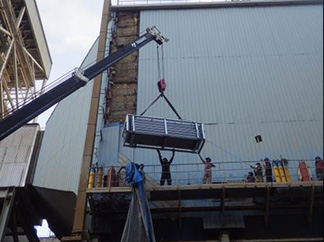
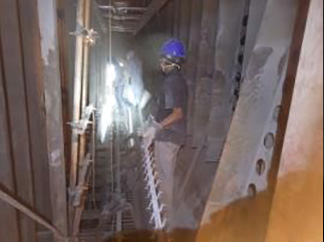
As a result, users were extremely satisfied with Tai & Chyun’s performance and RDE quality that another RDE replacement was done for the other 10 fields in 2018 with mechanical maintenance works for 16 fields also included.
During the project, 12,800 pcs of RDE were installed with technical direction from our experienced engineers. The maintenance and corrective actions recommended from the previous findings during inspection were also carried out before the RDE replacement for this shutdown, which comprised of CE system, CE rapping system, DE system and DE rapping system.
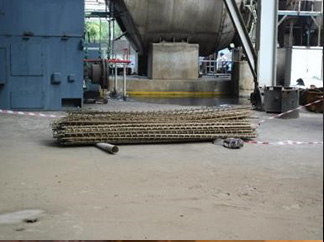
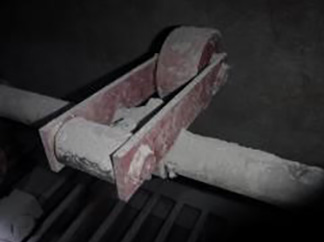
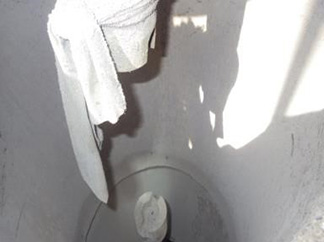
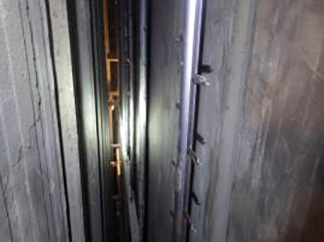
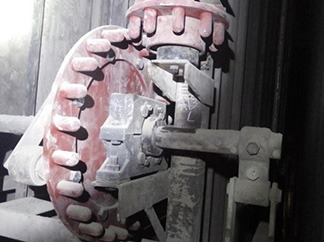
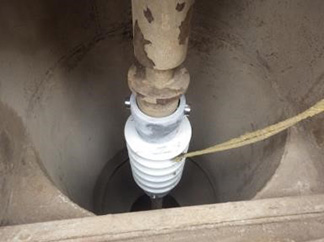
Benefit
RDE is one of the solutions that has been commercialized and proven to increase ESP dust collection efficiency. The new RDE reduces the problems of breakage and bent spike and allows for superior corona generation to help improve voltage stream and better dust collection efficiency. Good part quality also extends its lifetime and lowers the frequency of maintenance. Below data illustrates an increase in kV and mA after new RDE installation.
After RDE replacement and mechanical maintenance, all parts are in good condition. The emission was reduced by more than 50% even with higher capacity of the boiler.
Data | Before
(4 November 2017) |
After
(8 April 2018) |
Emission | 137 mg/Nm3 | 62.58 mg/Nm3 |
Load | 500 MW | 625 MW |
*Average emission comparison
Phase | Phase I (2015) | Phase II (2016) | Phase III (2018) |
Work Scope | Inspection and part measurement | Rigid Discharge Electrode Replacement and Measurement | Rigid Discharge Electrode Replacement and Mechanical Maintenance |
Location | All | 2 Fields | RDE: 10 Fields
Mechanical Maintenance: 16 Fields |
Duration | 5 days | 20 days | 25 days |
Result | kV/mA Improved
1st Field: 25% kV, 321% mA |
Emission Reduction: 54% |
ESP Improvement Result