ESP Overhaul with Corten CE in Sugar Plant
Application
Industry: Biomass
ESP OEM / Information: TENGY Group Co.
Process: Power generation from bagasse
Country: Northeastern part of Thailand
Problem
The sugar plant faced severe corrosion problem inside their ESP. The internal parts including Gas Distribution (GD) screen and all 3 fields of Collecting Electrode (CE) and Rigid Discharge Electrode (RDE) were deteriorated and corroded. Some fields tripped and could no longer operate. These led to ESP underperformance and resulted in emission issue.
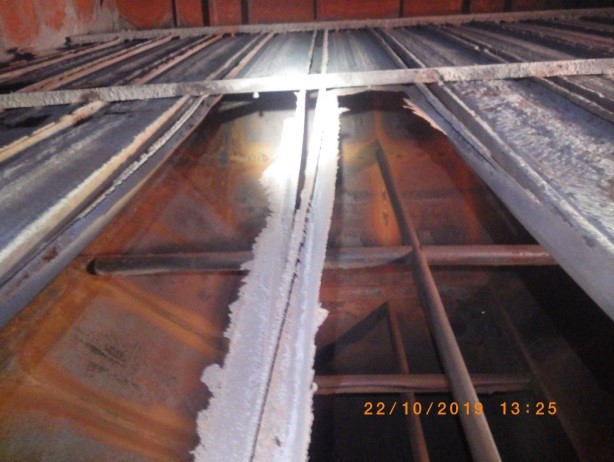
Corroded GD screen
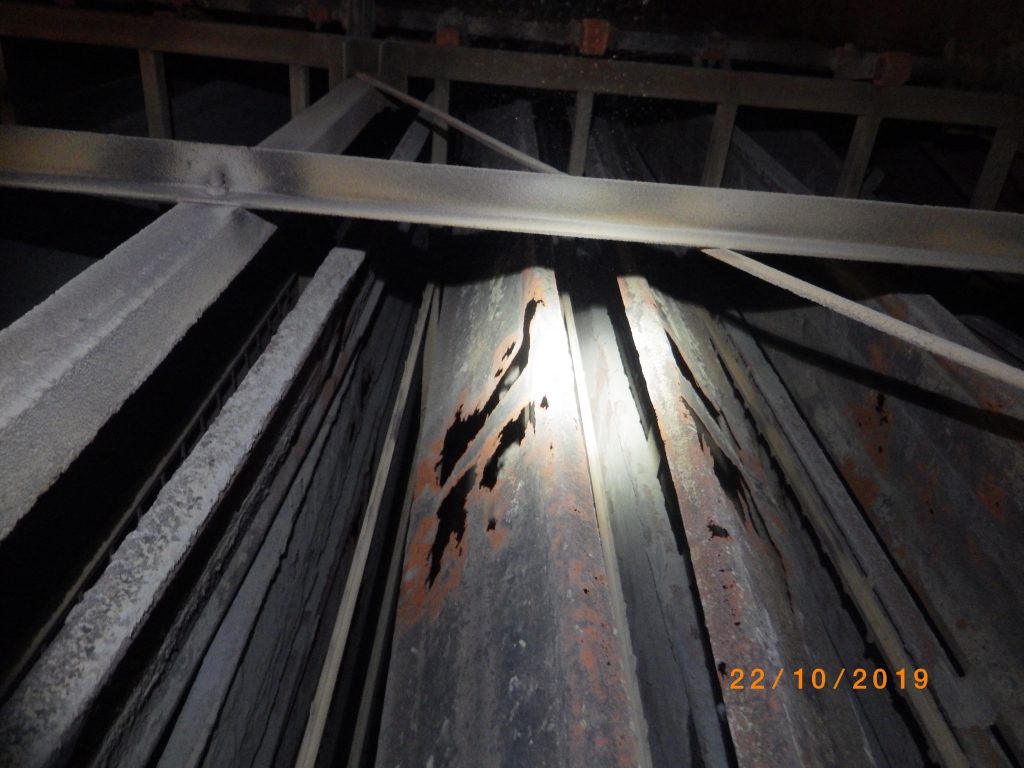
Corroded CE
Upon inspection, it had been found that the root cause of corrosion was air leakage from the access doors and insulator compartments. In addition, air leakage from multi cyclone caused the inlet temperature of the ESP to drop below 100°C allowing moisture to form inside the ESP. There were also fallen and bent DE and CE that came into contact with each other leading to ESP trip.
Solution
ESP overhaul would be implemented along with fixing of multi cyclone leakage. Tai & Chyun had been awarded for ESP overhaul that included complete CE and RDE replacement and maintenance. All CE and RDE in the 3 fields were renewed. CE in the 1st and 2nd field, in particular, were made of Corten steel material to withstand corrosion from high flue gas concentration in the inlet. Maintenance and replacement of some other internal parts such as rapping system and access door gasket were also carried out in this project.
Tai & Chyun was imposed with certain challenges during the project execution especially from dismantling the severely corroded GD screen and CE in some areas of the ESP that made them impossible to be removed out of the rooftop as usually done before. Therefore, the corroded parts must be cut before being removed out of the access door instead, which might have had affected the shutdown period. Nevertheless, with good management and proper supervision, the replacement project was completed on time in compliance with the plant’s shutdown schedule.
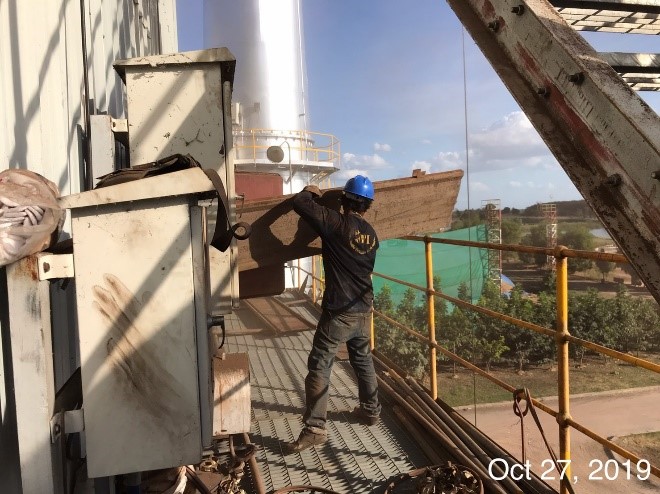
Dismantled CE being removed out of the access door
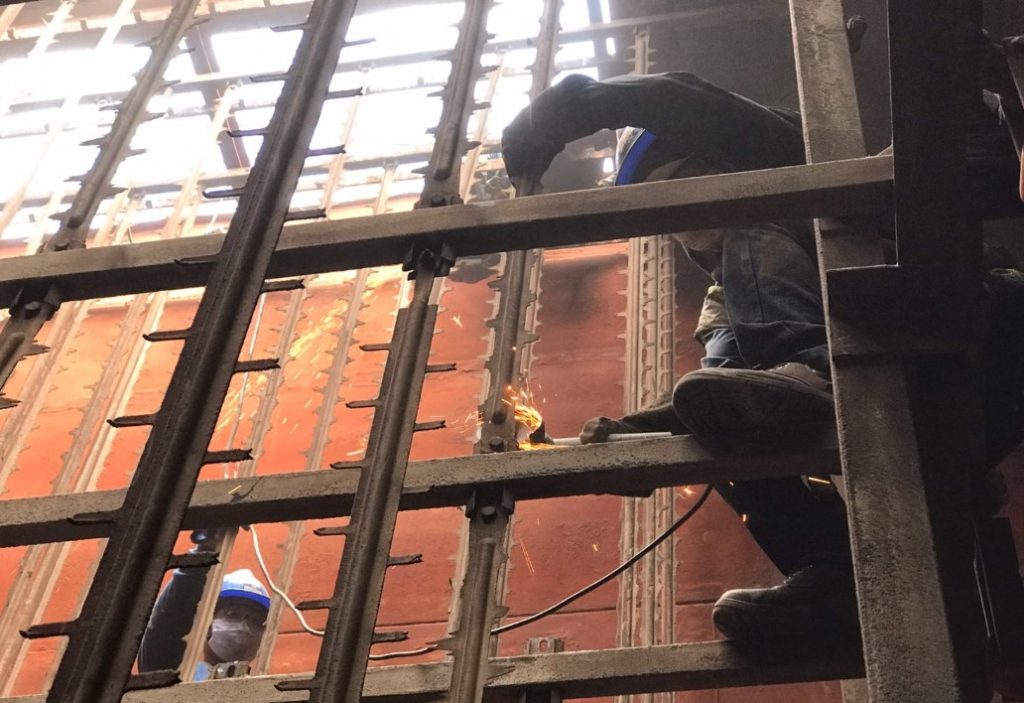
Dismantling old RDE
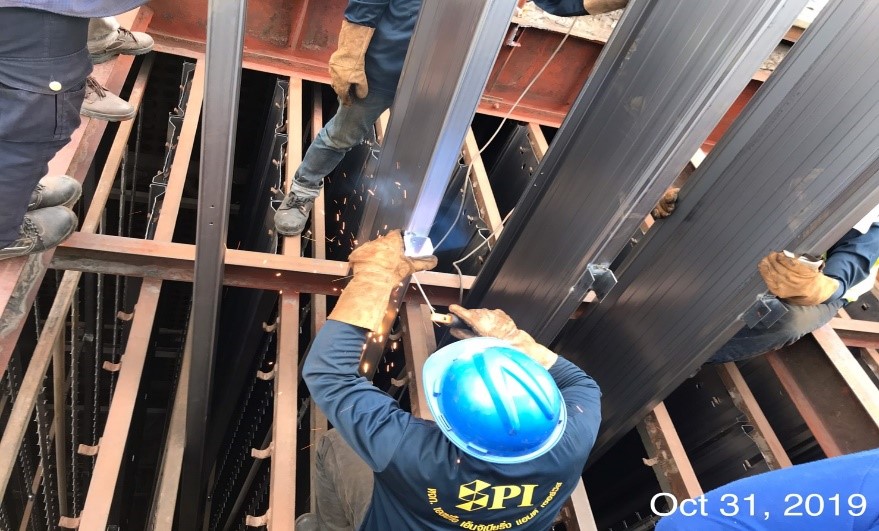
Installing new CE
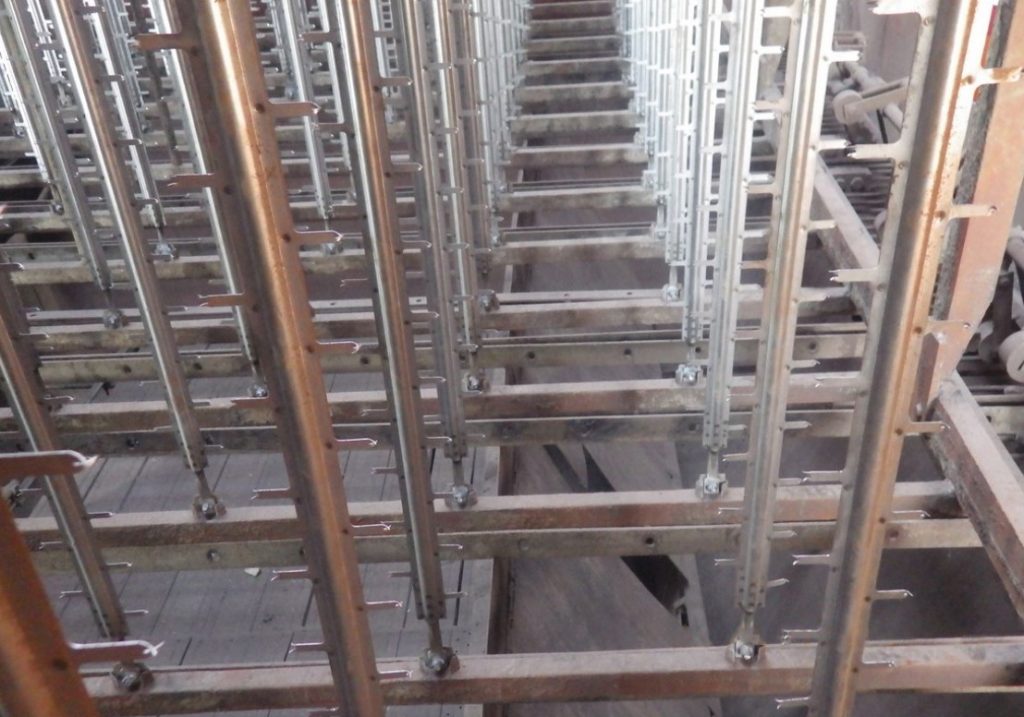
Newly installed RDE
Benefit
After the replacement project, all 3 fields of the ESP were back to normal operation without any tripping issue. The plant had not experienced any emergency shutdown due to ESP problem after operating for 5 months straight. Inspection was done on the ESP and revealed that CEs were still in good condition with no sign of corrosion or leakage compared to the old CE that had only lasted for 3 months.
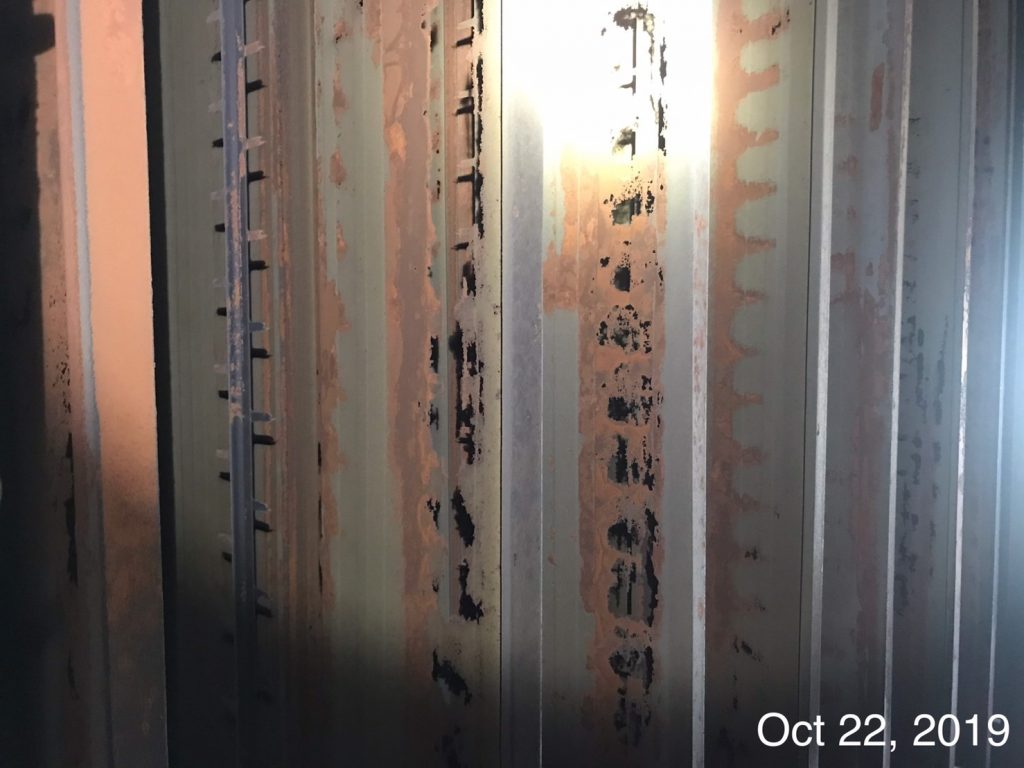
Old CE after 3 months of operation
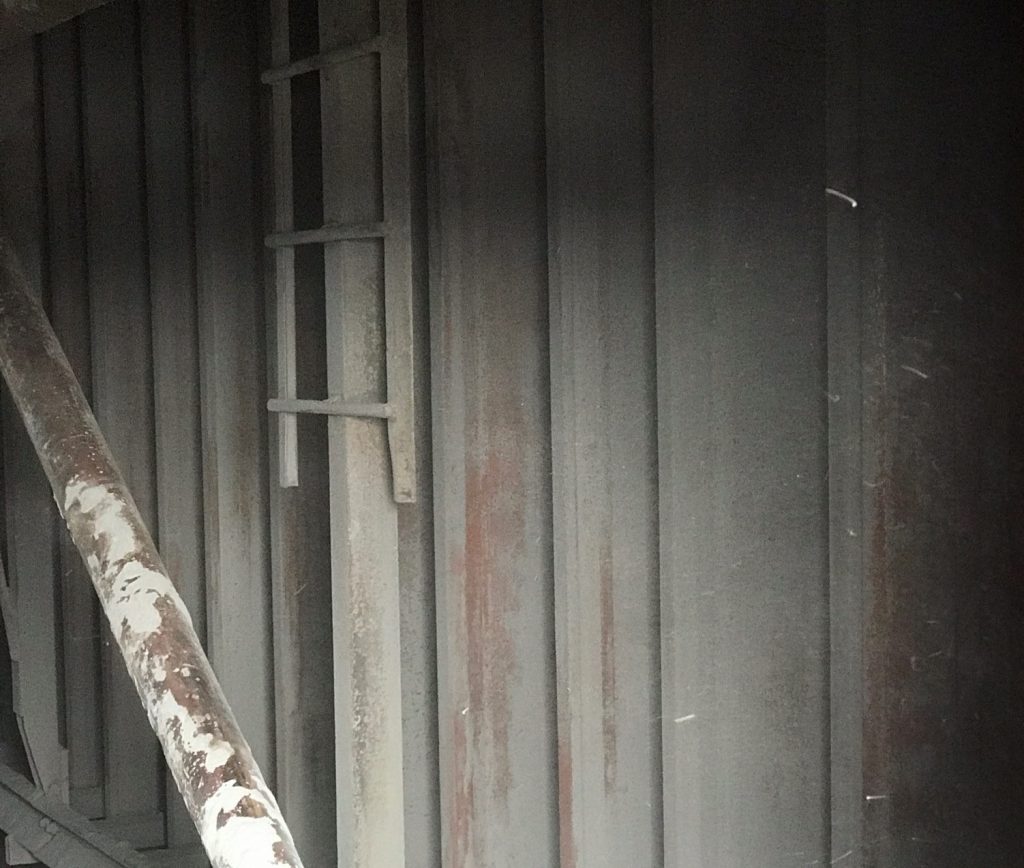
New CE after 5 months of operation