Collecting Electrode & Discharge Electrode Retrofit in a Cement Plant
Application
Industry: Cement
Capacity: 1,600TPD
ESP OEM / Information:
OEM: Korea Cottrell
Process: Raw Mill / Kiln
Start of Operation: 1995
Original Type of Electrodes: CE (Sword type), DE (Dura-Trode)
Rapping Design: MIGI Rapper for both CE and DE
Country: Philippines
Problem
Past inspections in the Kiln ESP revealed a major issue as the unit showed signs of aging parts. Collecting Electrode (CE) and Discharge Electrode (DE) systems had started to deteriorate resulting in poor collecting efficiency. Furthermore, such CE and DE designs were obsolete and not anymore available in the market.
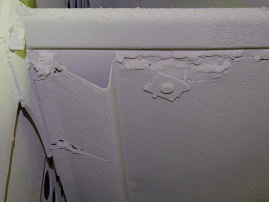
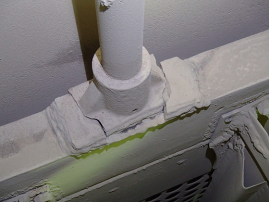
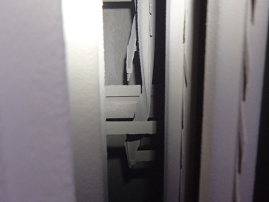
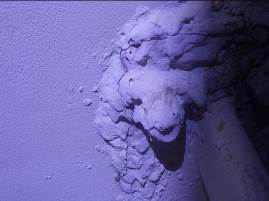
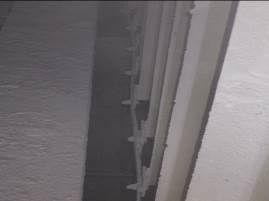
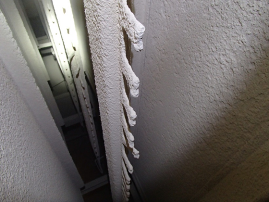
Solution
Due to design obsolescence, Tai & Chyun proposed to retrofit Dura-Trode DE to Pipe and Spike type and CE to a more improved design. Pipe and Spike DE design provides more aggressive corona current generation particularly at high dust loading. The installation was carried out at the inlet field to handle the heavier dust load.
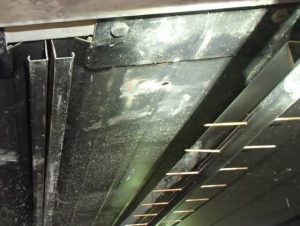
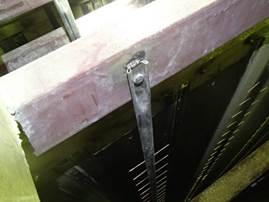
New design of CE and DE
Benefit
The retrofit to Rigid DE and new CE design allowed the ESP to operate reliably thus preventing emergent or unnecessary shutdowns due to broken / damaged internal parts. Such retrofit also helped the plant keep their emission level below regulation limits and so continuous smooth production could be achieved.
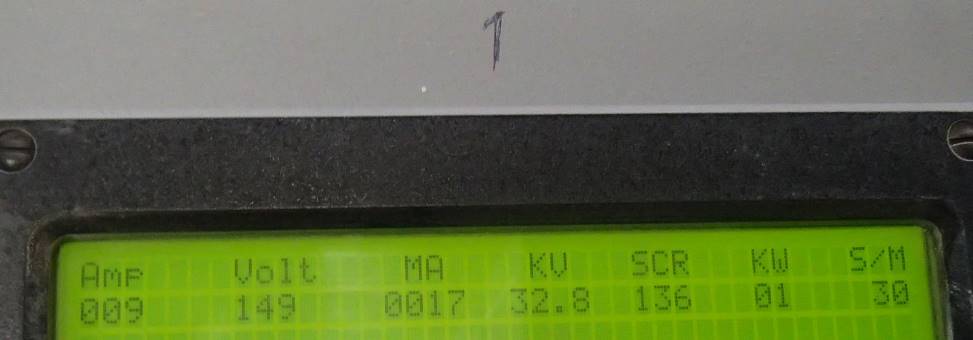
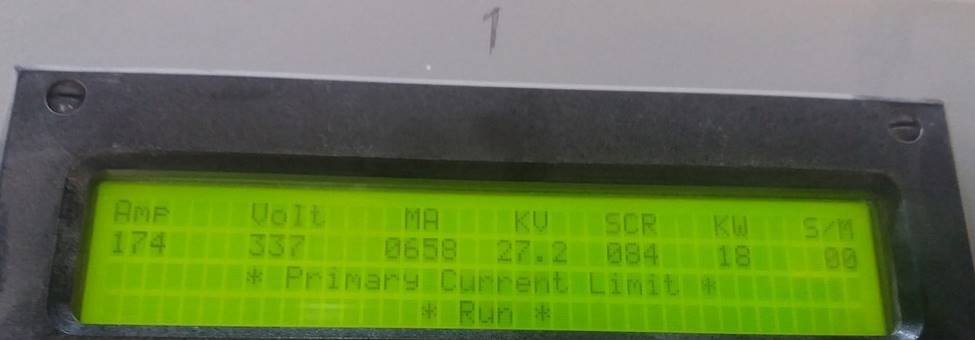
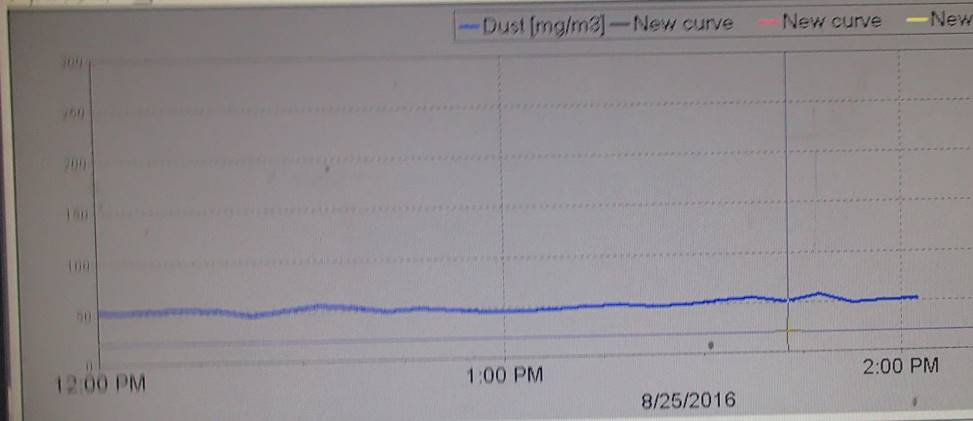