Application
Cooler ESP of a cement plant in Vietnam
Problem
1.Dust build-up was observed on inlet Gas Distribution (GD) Screen, Collecting Electrode (CE) and Discharge Electrode (DE), which led to high sparking during operation.
2.Discharge Electrodes were damaged and broken, which caused short-circuit.
3.Customer expected to reduce their emission from 60mg/Nm3 to less than 20mg/Nm3.
Solution
Tai & Chyun recommended replacing CE and DE for 2 fields as well as upgrading Conventional T/R into High Frequency T/R for the 1st and 2nd field. In addition, maintenance and supervision were also performed during the outage. The installation was completed within 25 days as below work scope:
1.Replacing Collecting Electrodes and Discharge Electrodes for the 2nd and 3rd field.
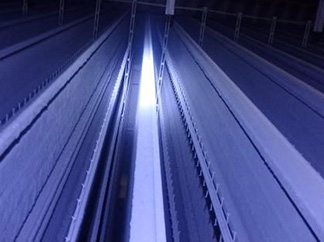
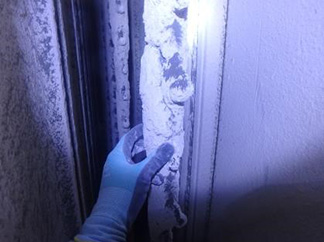
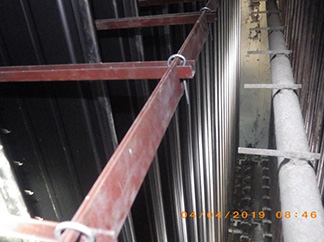
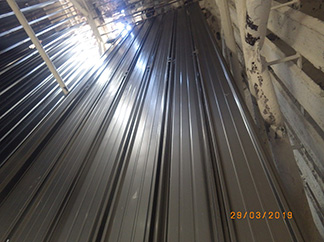
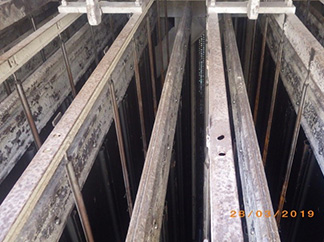
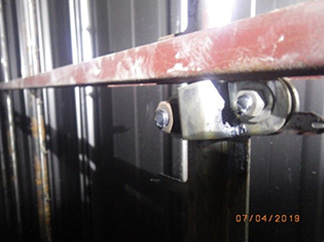
2.Installing new GD screen at ESP inlet.
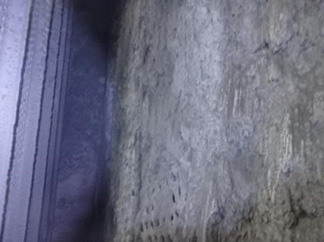
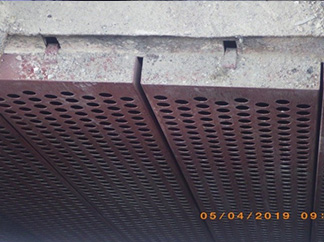
3.Upgrading into new High Frequency T/R for the 1st and 2nd field.
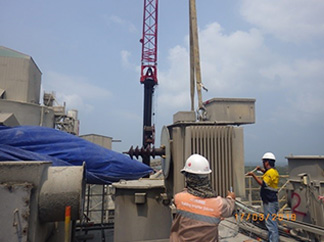
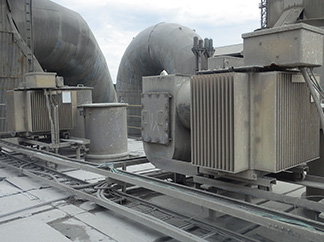
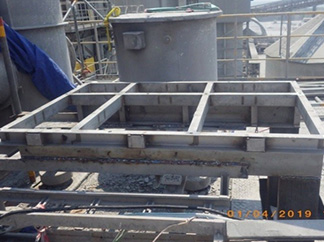
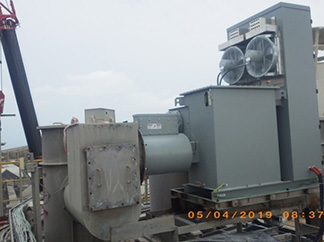
Benefit
New RDE and maintenance recovered ESP performance. With High Frequency T/R upgrade, ESP collection efficiency increased and reached the emission reduction target of less than 20mg/Nm3. Meanwhile, the gas volume also increased with comparison to that before the overhaul and thus exceeded customer expectation.
March 2018 | May 2019 | |
Gas volume m3/h | 324,000 | 414,000 |
Production capacity T/D | 4000 | 4339 |
Emission mg/Nm3 | 60 | 15 |
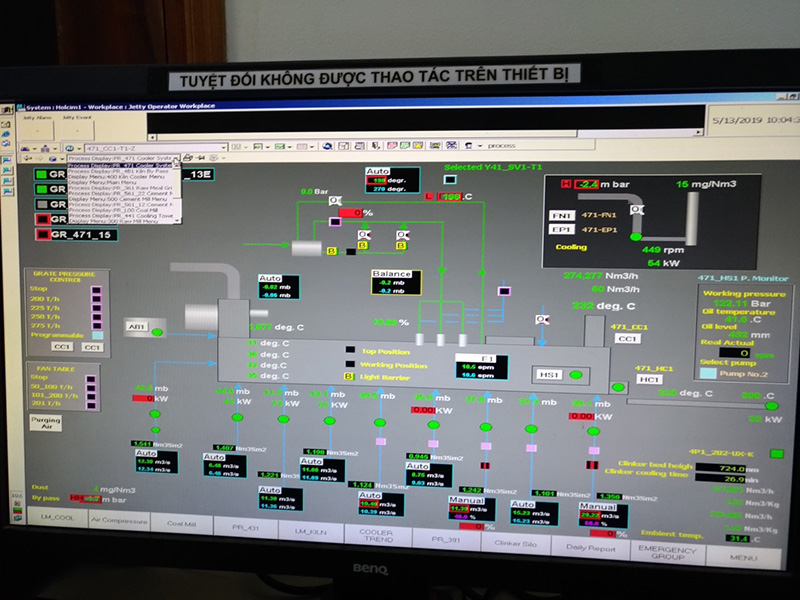
Result from electrical readings also showed significant improvement in power output, which is increased secondary voltage (kV) and secondary current (mA). As shown in the below tables, ESP could only operate at low power output due to heavy sparking before the overhaul. After the upgrade, ESP could produce more power output indicating ESP dust collection efficiency also increased.
Before Retrofit (Oct 2018)
Field 1 | Field 2 | Field 3 | |
kVmean | 11 | 18 | 44 |
mA | 30-40 | 25-40 | 50-70 |
After Retrofit (May 2019)
Field 1 | Field 2 | Field 3 | |
kVmean | 31 | 32 | 24 |
mA | 60-80 | 140-170 | 130-170 |