Ash Handling System Retrofit – Dilute Phase
Application
Industry: Power, 12-MW unit
Process: ESP fly ash handling system
Country: Indonesia
Problem
The plant’s existing design of ESP fly ash handling system is dilute phase type, with roots blower as air conveying source and 3 rotary feeders (3 ESP hoppers) feeding ash into the pipeline. For maintenance purpose, in the original design, an ash pipe under each hopper (total of 3 ash pipes with sizes of 2”, 2 1/2”, and 4”) joined at 5” pipeline leading up to silo. From design aspect, not only the conveying air volume from roots blower was too low to create enough air velocity inside the 5” pipeline but also the conveying air couldn’t be distributed evenly to the 3 pipelines. As a result, ash often found clogged at the 3-to-1 pipeline intersection. Severe leakages were also found at rotor blades of the existing rotary valves, which aggravated the issue as leaked air hindered the gravity flow of ash into the feeder. Furthermore, the vent filter on top of silo was out of function due to lack of maintenance.
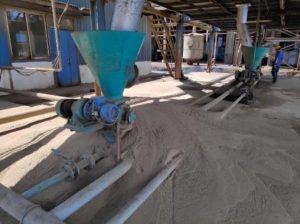
Ash handling system failure – ash being drained onto the ground
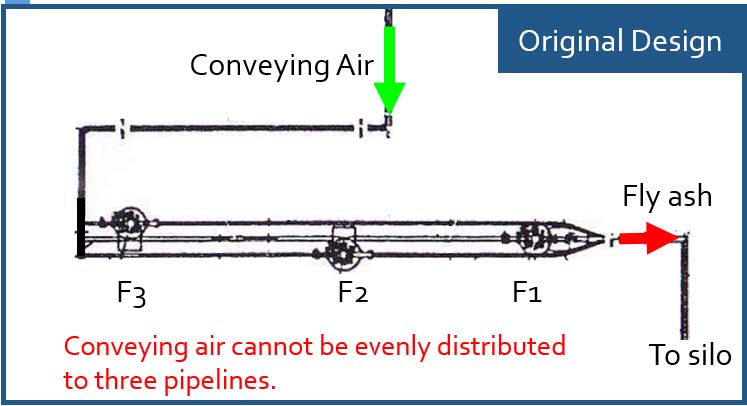
Original design
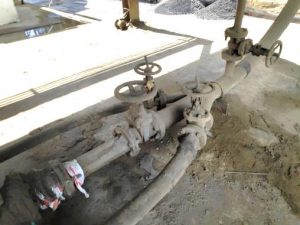
Clogging at 3-to-1 pipeline intersection
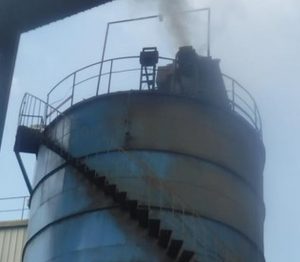
Ash leaking from vent filter
Solution
Tai & Chyun provided customized solution per the plant’s planned budget. Major features are listed as below:
1.Replace the 5” pipeline with two 4” pipelines:
As majority of ash is collected in ESP field 1, one new pipe has been installed for field 1 ash (Line 1), while field 2 & 3 share the other pipe (Line 2). In addition, bypass pipes have been installed in case of when troubleshooting in only one of the fields is needed. The elbow pipes are ceramic-sleeved so they are wear-resistant and have longer lifetime.
2.Provide sufficient conveying air:
Independent conveying air source has been provided for Line 1 and Line 2. For Line 1, two new roots blowers with larger capacity were installed (one running, one standby). For Line 2, existing blower was remained for use.
3.Increase silo vent filter filtration area:
In the new design, one new 4” pipe has been installed leading to silo. Since the plant had a plan of loading ash from another unit to the same silo in the near future, the total air volume will increase. Therefore, the new vent filter size had to be re-designed and installed.
Conclusion
Most of the installation job was prepared before shutdown, pipe length measured, cut, and assembled. Actual installation only took around 10 days during shutdown period. After the retrofit, ash can be conveyed smoothly and automatically to the silo. The plant no longer has to drain the ash onto the ground and clean manually. The new pipeline design allows more operation flexibility and reserves buffer for future additional loading to the silo. Customer was extremely satisfied with the result.
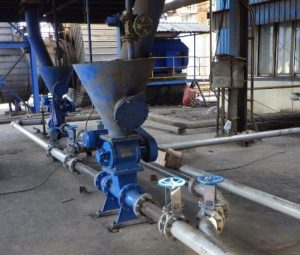
Newly installed rotary valve
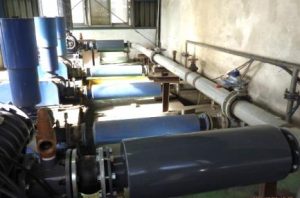
New roots blower
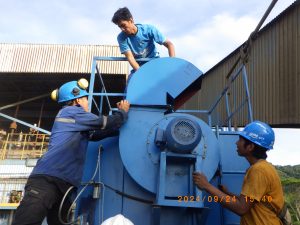
New vent filter