Upgrade of Ash Conveying System from Hydraulic to Pneumatic
Application
Industry: Power
Process: Economizer (ECO), Air Pre-Heater (APH)
Country: Taiwan
Problem
The power plant has been in operation for more than 40 years with total of 10 coal-fired units of capacity 550MW each. Ashes from ECO and APH were conveyed via sea- water to the ash pond and by then the ash pond was almost full. Thus, the plant was looking for an alternative solution to ash disposal.
Challenge
Pneumatic ash conveying system has been well known in the market for decades for its reliability, easy maintenance and simple routing. Therefore, pneumatic conveying system has been chosen for this case instead of mechanical or hydraulic. It turned out that determining a new destination for ECO / APH ash disposal was the most challenging part of this project.
Pneumatic conveying system is composed of four major elements: air mover, feeding / mixing device, pipe, and gas / dust separation device (bag filter). It is costly to build a new silo with bag filter and available space is limited. The existing bottom ash silo was not an option either since the bottom ash is wet and very humid in the silo. If a new bag filter were set up for ECO / APH ash on top of the bottom ash silo, the moisture would damage the filter bags after some time of operation. Upon site survey and weighing a few available options, Tai & Chyun came to a conclusion that the best solution was to convey the ECO / APH ash to the Submerged Chain Conveyor (SCC).
Solution
The new pneumatic conveying system layout is shown below. We provided 2 new air compressors (one running and the other stand-by), 14 blow tanks with inlet and discharge valves, pipelines, and bag filter with accessories.
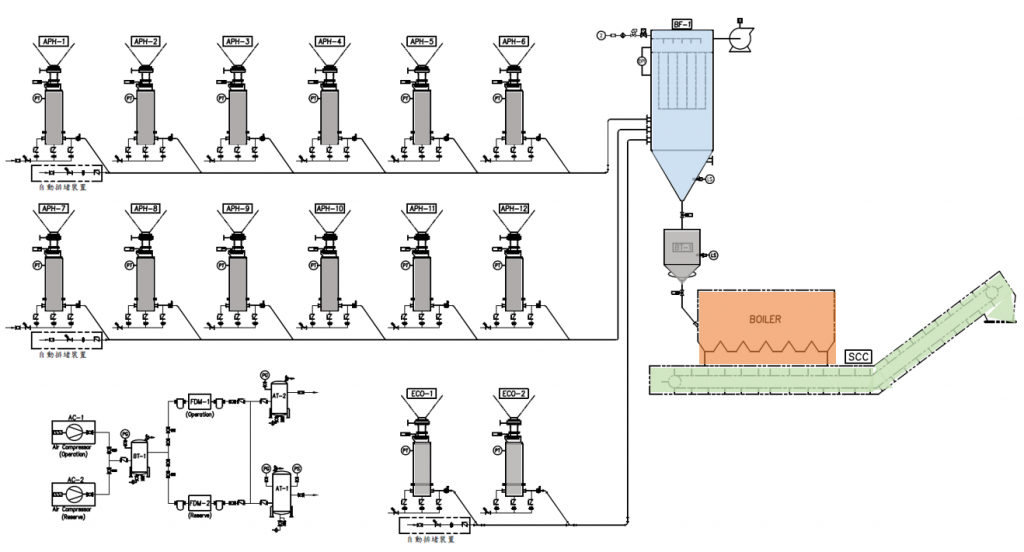
FEATURE
1.Bottom-discharge blow tank
ECO / APH ashes are coarser than ESP fly ash and possess poor permeability. Therefore, it is more suitable to apply bottom-discharge blow tank instead of top-discharge blow tank that is commonly seen in ESP ash handling system.
2.The inlet/discharge valves are rotating disc valves with tungsten plated disc.
A tungsten seal plate is applied to the disc, and the top/bottom portion of the valves
which contacts the disc are also made of tungsten seal ring. It can sustain constant abrasion from ash. A spring is used to support the disc. When the valve opens/closes, the disc can spin freely to allow even abrasion of the seal ring.
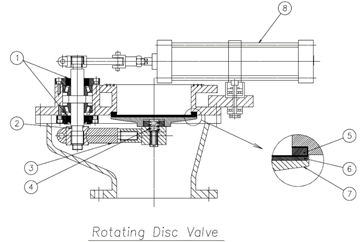
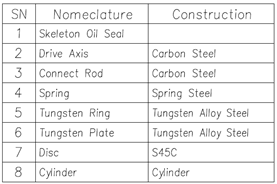
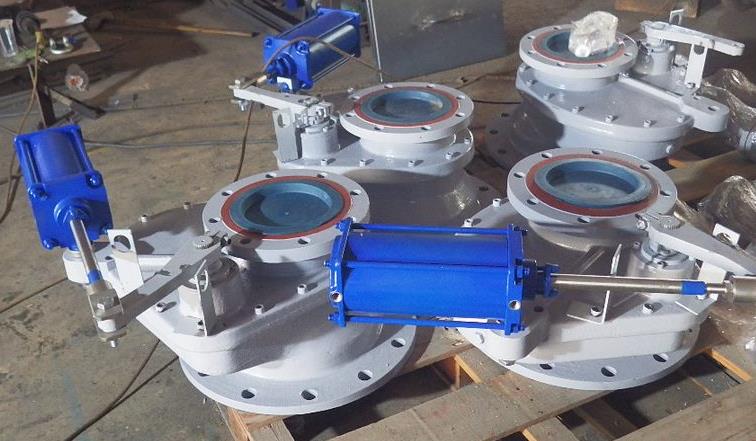
3.The elbow pipes are with ceramic sleeve and large bend radius (10D)
By increasing the bend radius to 10D, the bend to pipe diameter ratio (D/d) is increased and the particle impact angle is decreased, and thus the abrasion is kept to the minimum. The hardness of ceramic liner is 9 MOHS, which also allows longer lifetime of the bend pipe.
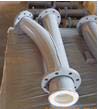
4.Buffer tank between bag filter and SCC to block moisture
Buffer tank with fluidization between bag filter outlet and SCC reduces the risk of moisture from traveling up the bag filter that leads to bag clogging.
Benefit
Project execution was initiated in unit 9 and took around 45 days to complete. By switching from hydraulic to pneumatic conveying system, the ECO / APH ash can now be disposed together with bottom ash within enclosed ash pipeline and so the surroundings are cleaner. The robust design of the valves and ceramic elbow pipes allow less maintenance cost and provide longer lifetime.
The results were satisfactory and the same system was also later applied to units 4, 10, 1, 7, 2, 3, and 8 respectively during shutdowns over the course of 3 years with minor modifications done to each unit depending on its existing design. For example, the bottom ash in unit 3 and 4 is conveyed in dry type of conveyor so no moisture is present in the bottom ash silo. Therefore, the ECO / APH ash of unit 3 and 4 can be conveyed directly to bottom ash silo.
Picture

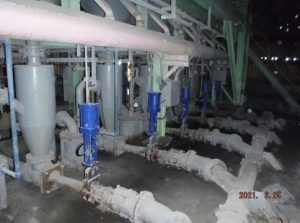
ECO tank
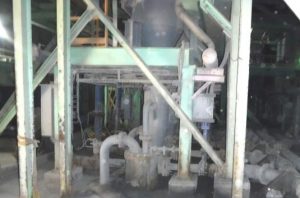
After retrofit
APH tank

ECO tank
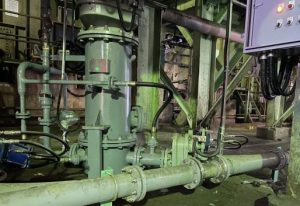
SCADA modification
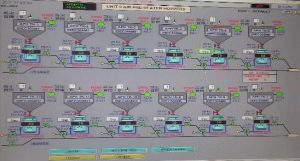
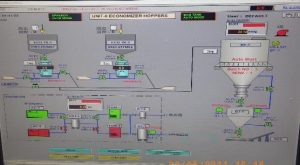
New air compressor, dryer, and air tank
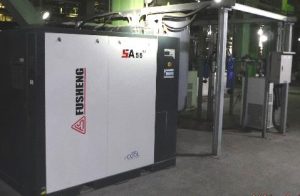
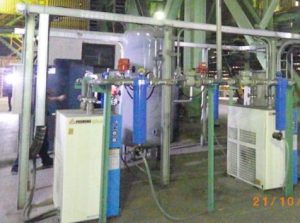
New bag filter with buffer tank
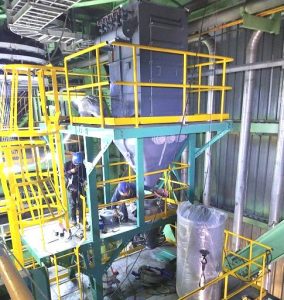